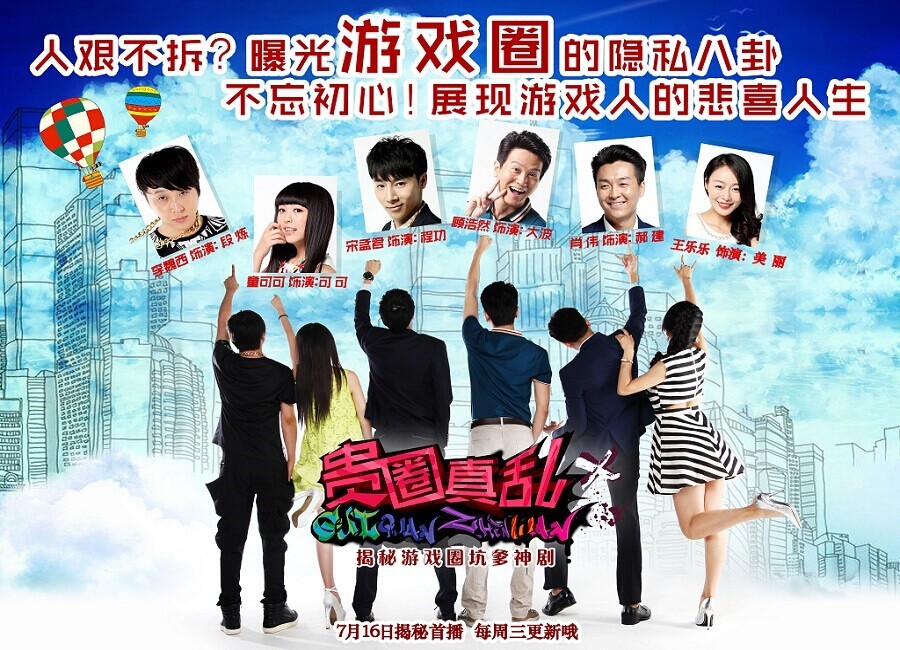
主程序是整个程序的核心,负责控制程序的整体流程,包括以下几个主要任务:
- 初始化:主程序首先要初始化程序的环境,包括加载必要的模块、设置全局变量等。
- 校验:主程序对输入的数据进行校验,确保数据的正确性,防止程序出现错误。
- 显示结果:主程序将处理后的结果显示给用户,可以是文本、图像或其他形式。
主程序与其他模块的关系
主程序通常与其他模块协作完成任务,其关系如下:
重用和可维护等原则,以便创建高质量、易于维护的程序。数控系统的工作流程:1、输入:零件程序及控制参数、补偿量等数据的输入,可采用光电阅读机、键盘、磁盘、连接上级计算机的DNC接口、网络等多种形式。 CNC装置在输入过程中通常还要完成无效码删除、代码校验和代码转换等工作。 2、译码:不论系统工作在MDI方式还是存储器方式,都是将零件程序以一个程序段为单位进行处理,把其中的各种零件轮廓信息(如起点、终点、直线或圆弧等)、加工速度信息(F代码)和其他辅助信息(M、S、T代码等)按照一定的语法规则解释成计算机能够识别的数据形式,并以一定的数据格式存放在指定的内存专用单元。 在译码过程中,还要完成对程序段的语法检查,若发现语法错误便立即报警。 3、刀具补偿:刀具补偿包括刀具长度补偿和刀具半径补偿。 通常CNC装置的零件程序以零件轮廓轨迹编程,刀具补偿作用是把零件轮廓轨迹转换成刀具中心轨迹。 在比较好的CNC装置中,刀具补偿的工件还包括程序段之间的自动转接和过切削判别,这就是所谓的C刀具补偿。 4、进给速度处理:编程所给的刀具移动速度,是在各坐标的合成方向上的速度。 速度处理首先要做的工作是根据合成速度来计算各运动坐标的分速度。 在有些CNC装置中,对于机床允许的最低速度和最高速度的限制、软件的自动加减速等也在这里处理。 5、插补:插补的任务是在一条给定起点和终点的曲线上进行“数据点的密化”。 插补程序在每个插补周期运行一次,在每个插补周期内,根据指令进给速度计算出一个微小的直线数据段。 通常,经过若干次插补周期后,插补加工完一个程序段轨迹,即完成从程序段起点到终点的“数据点密化”工作。 6、位置控制:位置控制处在伺服回路的位置环上,这部分工作可以由软件实现,也可以由硬件完成。 它的主要任务是在每个采样周期内,将理论位置与实际反馈位置相比较,用其差值去控制伺服电动机。 在位置控制中通常还要完成位置回路的增益调整、各坐标方向的螺距误差补偿和反向间隙补偿,以提高机床的定位精度。 7、I/0处理:I/O处理主要处理CNC装置面板开关信号,机床电气信号的输入、输出和控制(如换刀、换挡、冷却等)。 8、显示:CNC装置的显示主要为操作者提供方便,通常用于零件程序的显示、参数显示、刀具位置显示、机床状态显示、报警显示等。 有些CNC装置中还有刀具加工轨迹的静态和动态图形显示。 9、诊断:对系统中出现的不正常情况进行检查、定位,包括联机诊断和脱机诊断。 数字控制系统简称,英文名称为NumericalControlSystem,早期是与计算机并行发展演化的,用于控制自动化加工设备的,由电子管和继电器等硬件构成具有计算能力的专用控制器的称为硬件数控(HardNC)。 20世纪70年代以后,分离的硬件电子元件逐步由集成度更高的计算机处理器代替,称为计算机数控系统。 计算机数控(Computerizednumericalcontrol,简称CNC)系统是用计算机控制加工功能,实现数值控制的系统。 CNC系统根据计算机存储器中存储的控制程序,执行部分或全部数值控制功能,并配有接口电路和伺服驱动装置,用于控制自动化加工设备的专用计算机系统。 CNC系统由数控程序存储装置(从早期的纸带到磁环,到磁带、磁盘到计算机通用的硬盘)、计算机控制主机(从专用计算机进化到PC体系结构的计算机)、可编程逻辑控制器(PLC)、主轴驱动装置和进给(伺服)驱动装置(包括检测装置)等组成。 由于逐步使用通用计算机,数控系统日趋具有了软件为主的色彩,又用PLC代替了传统的机床电器逻辑控制装置,使系统更小巧,其灵活性、通用性、可靠性更好,易于实现复杂的数控功能,使用、维护也方便,并具有与网络连接及进行远程通信的功能。
本文原创来源:电气TV网,欢迎收藏本网址,收藏不迷路哦!
添加新评论