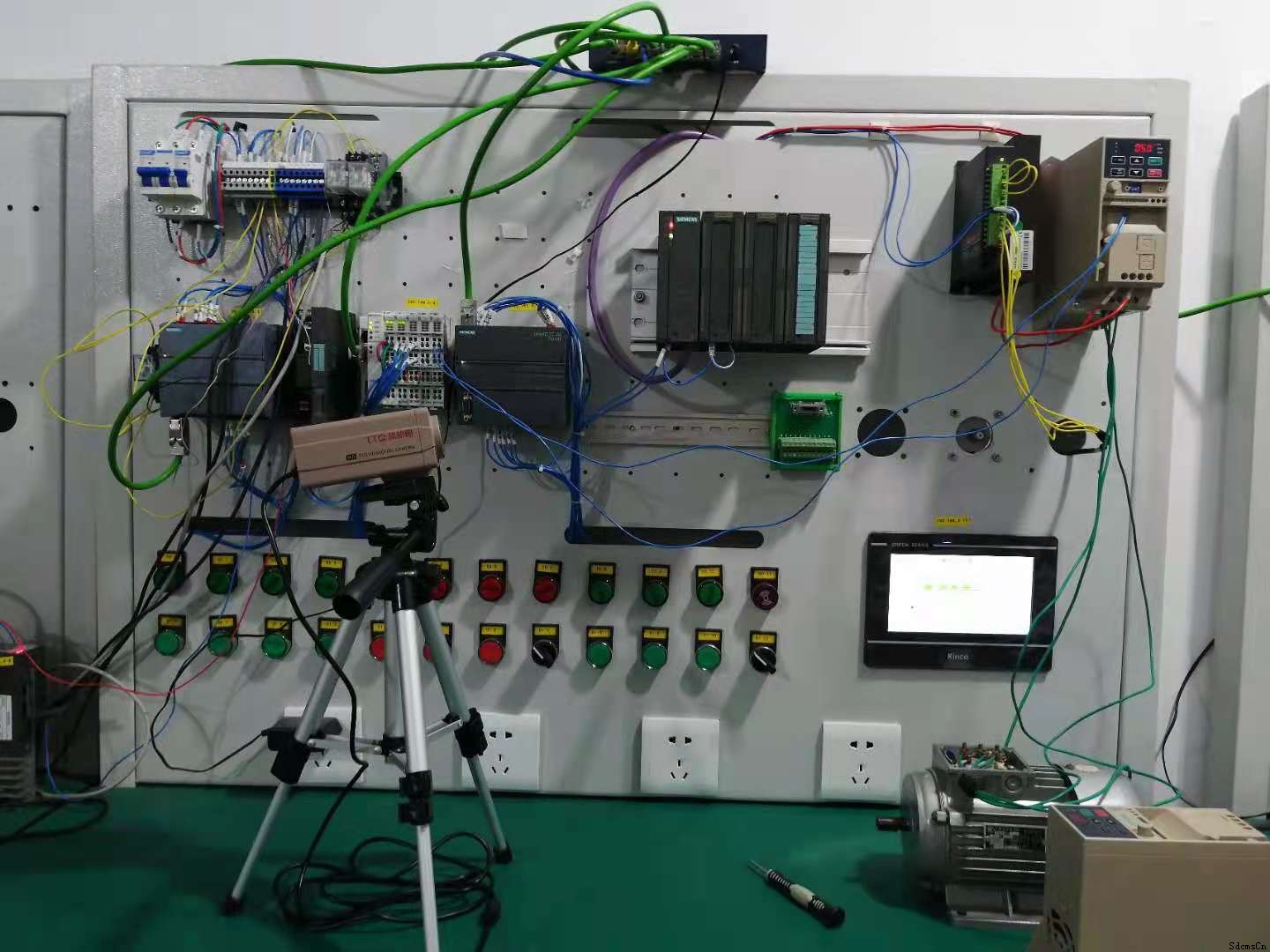
简介
PLC(可编程逻辑控制器)是工业自动化系统中必不可少的组件,可用于控制机器和过程。与任何电子设备一样,PLC 也会遇到错误和故障。诊断和解决这些错误对于保持系统正常运行至关重要。PLC 错误类型
PLC错误可以分为以下几类:- 硬件错误:由物理损坏或故障引起的错误,例如电源故障、连接松动或损坏的组件。
- 软件错误:由编程错误或系统配置问题引起的错误,例如指令错误、内存溢出或通信问题。
- 应用程序错误:由用户编程的应用程序中的逻辑错误引起的错误,例如输入或输出信号不正确或控制算法缺陷。
PLC 自诊断功能
大多数现代 PLC 具有自诊断功能,可以检测和报告错误。这些功能通常包括:- 状态指示灯:指示 PLC 的当前状态,例如运行、停止、故障或诊断模式。
- 错误代码:特定的代码,用于识别特定错误或故障。
- 诊断信息:提供有关错误原因和位置的详细信息。
诊断 PLC 错误的过程
诊断 PLC 错误需要遵循以下步骤:1. 观察状态指示灯:检查 PLC 的状态指示灯,确定其当前状态。2. 查看错误代码:从 PLC 的显示屏或 HMI(人机界面)中读取错误代码。3. 查找错误描述:使用 PLC 的用户手册或在线文档查找与错误代码对应的错误描述。4. 分析诊断信息:如果 PLC 提供诊断信息,请仔细分析信息以确定错误的根本原因。5. 检查硬件:如果错误代码表明硬件故障,请检查电力连接、连接和组件,是否有损坏或松动。6. 检查软件:如果错误代码表明软件错误,请检查程序代码是否有语法错误、内存溢出或通信问题。7. 修复错误:根据诊断结果,修复错误可能涉及更换损坏的组件、修改软件代码或解决应用程序中的逻辑问题。解决常见 PLC 错误
以下是一些常见的 PLC 错误及其可能的解决方案:- 输入/输出错误:检查输入/输出模块、传感器和执行器的连接和配置。
- 通信错误:检查通信线缆、端口设置和协议配置。
- 内存溢出:优化程序代码,减少内存使用,或使用具有更多内存的 PLC。
- 指令错误:检查程序代码中使用的指令是否正确,并确保它们以正确的顺序执行。
- 逻辑错误:仔细检查程序代码,确保控制算法正确且没有逻辑缺陷。
预防 PLC 错误
可以采取以下措施来预防 PLC 错误:- 定期维护:定期检查 PLC 及其组件,确保其处于良好的工作状态。
- 仔细编程:遵循良好的编程实践,避免语法错误、内存溢出和逻辑缺陷。
- 测试和验证:在将程序部署到 PLC 之前,彻底测试和验证其功能。
- 使用高质量组件:使用可靠的组件和连接,以最大程度地减少硬件故障的可能性。
结论
诊断和解决 PLC 错误对于保持工业自动化系统正常运行至关重要。通过了解 PLC 错误类型、自诊断功能以及诊断和解决错误的过程,可以有效地排除故障并恢复操作。遵循预防性措施,例如定期维护、仔细编程和测试,还可以最大程度地减少 PLC 错误的发生。本文原创来源:电气TV网,欢迎收藏本网址,收藏不迷路哦!
添加新评论