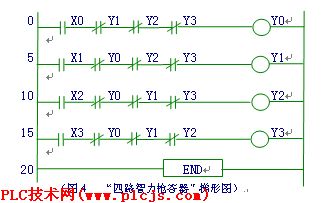
一、引言
在现代工业自动化控制系统中,可编程逻辑控制器(PLC)扮演着至关重要的角色。
PLC作为一种数字计算机控制器,广泛应用于各种生产设备和工艺流程中,以实现自动化、智能化控制。
在PLC程序中,负反馈机制是确保系统稳定、精确运行的关键环节。
本文将详细探讨PLC程序中的负反馈机制,帮助读者更好地理解其原理及应用。
二、PLC概述
PLC,即可编程逻辑控制器,是一种专门为工业环境设计的数字计算机控制器。
PLC具有高度的灵活性和可靠性,能够完成各种逻辑控制、运动控制、数据处理等任务。
在工业生产中,PLC广泛应用于机床、生产线、机器人等设备的控制。
三、负反馈机制在PLC程序中的作用
在PLC程序中,负反馈机制主要用于调节和控制系统的运行状态,确保系统稳定、精确运行。负反馈机制的作用包括以下几个方面:
1. 纠正误差:通过负反馈,PLC系统可以实时监测实际运行状态与设定目标之间的偏差,并据此调整输出,以纠正误差。
2. 稳定系统:负反馈有助于抑制系统内部的干扰和噪声,使系统保持稳定状态。
3. 提高精度:通过精确调节输出,负反馈可以提高系统的控制精度。
四、PLC程序中负反馈机制的实现
在PLC程序中,负反馈机制的实现主要依赖于反馈信号和比较环节。
1. 反馈信号:从系统输出端获取实际运行状态的信息,形成反馈信号。反馈信号可以是电压、电流、电阻、温度等物理量的变化。
2. 比较环节:将反馈信号与设定目标进行比较,得出偏差信号。偏差信号将被用于调节系统的输出。
在PLC程序中,负反馈机制的实现过程如下:
1. PLC根据输入信号(如传感器信号)获取实际运行状态的信息。
2. PLC将获取的实际状态信息与设定目标进行比较,得出偏差信号。
3. PLC根据偏差信号,通过算法计算得出控制信号。
4. PLC将控制信号输出到执行机构,调节系统的运行状态。
5. 执行机构根据控制信号调整系统输出,产生新的实际状态信息。
6. PLC再次获取新的实际状态信息,进入下一轮的比较和调节过程。
五、负反馈机制在PLC程序中的具体应用
1. 在机床控制中的应用:在机床加工过程中,PLC通过负反馈机制对机床的转速、温度、压力等参数进行实时监测和调节,确保机床的精确运行。
2. 在生产线控制中的应用:在生产线中,PLC通过负反馈机制对生产设备的运行状态进行实时监控,确保生产过程的稳定、高效进行。
3. 在机器人控制中的应用:在机器人运动中,PLC通过负反馈机制对机器人的位置、速度等参数进行精确控制,实现机器人的精准运动。
六、注意事项
在PLC程序中应用负反馈机制时,需要注意以下几点:
1. 准确获取反馈信号:确保反馈信号的准确性,以避免误差的累积。
2. 合理设置比较环节:比较环节的设置应考虑到系统的实际情况,以确保负反馈机制的有效性。
3. 调试与优化:在实际应用中,需要根据系统的运行情况对PLC程序进行调试与优化,以提高系统的性能。
七、结论
负反馈机制在PLC程序中具有重要作用,是实现系统稳定、精确运行的关键环节。
通过负反馈机制,PLC系统可以实时监测实际运行状态与设定目标之间的偏差,并据此调整输出,以纠正误差、稳定系统、提高精度。
在实际应用中,需要根据系统的实际情况合理设置比较环节,并注意反馈信号的准确性和程序的调试与优化。
仪表的反作用和plc的反作用区别
PLC指的是可编程控制器,它是一种专门为在工业环境下应用而设计的数字运算操作的电子装置。它采用可以编制程序的存储器,用来在其内部存储执行逻辑运算、顺序运算、计时、计数和算术运算等操作的指令,并能通过数字式或模拟式
调节器的正反作用当 PV>SV,MV 需要开大时为正作用;反之为反作用;以上判断是在假设阀门特性后进行的,假设阀门为气开阀或电开阀(正作用),调节器的正反作用由被控对象、负反馈即可判断:当 PV>SV 时, MV 需开大可知被控对象为负,调节器为正,构成负反馈;当 PV>SV 时, MV 需关小可知被控对象为正,调节器为负,构成负反馈。实际完整的判断方法为:
调节器的正反作用设置原理:
实际上, 调节器的正反作用通常根据PID 控制的闭环回路负反馈的原则设置。
(1)现场各种检测仪表一般都认为是正作用的;(不考虑其正反作用)
(2)气动调节阀门的正反特性由阀门定位器、执行机构的特性共同组成。
① 定位器的正反作用(不考虑其正反作用)输入信号4mA 时输出气压最小,输入信号是20mA 时输出气压最大,正作用;反之则为反作用。
PID与PLC控制的异同
PID控制目录[隐藏]概述基本用途现实意义PID控制实现[编辑本段]概述当今的自动控制技术都是基于反馈的概念。 反馈理论的要素包括三个部分:测量、比较和执行。 测量关心的变量,与期望值相比较,用这个误差纠正调节控制系统的响应。 这个理论和应用自动控制的关键是,做出正确的测量和比较后,如何才能更好地纠正系统。 PID(比例-积分-微分)控制器作为最早实用化的控制器已有50多年历史,现在仍然是应用最广泛的工业控制器。 PID控制器简单易懂,使用中不需精确的系统模型等先决条件,因而成为应用最为广泛的控制器。 PID控制器由比例单元(P)、积分单元(I)和微分单元(D)组成。 其输入e (t)与输出u (t)的关系为u(t)=kp(e((t)+1/TI∫e(t)dt+TD*de(t)/dt) 式中积分的上下限分别是0和t因此它的传递函数为:G(s)=U(s)/E(s)=kp(1+1/(TI*s)+TD*s)其中kp为比例系数; TI为积分时间常数; TD为微分时间常数[编辑本段]基本用途它由于用途广泛、使用灵活,已有系列化产品,使用中只需设定三个参数(Kp, Ti和Td)即可。 在很多情况下,并不一定需要全部三个单元,可以取其中的一到两个单元,但比例控制单元是必不可少的。 首先,PID应用范围广。 虽然很多工业过程是非线性或时变的,但通过对其简化可以变成基本线性和动态特性不随时间变化的系统,这样PID就可控制了。 其次,PID参数较易整定。 也就是,PID参数Kp,Ti和Td可以根据过程的动态特性及时整定。 如果过程的动态特性变化,例如可能由负载的变化引起系统动态特性变化,PID参数就可以重新整定。 第三,PID控制器在实践中也不断的得到改进,下面两个改进的例子。 在工厂,总是能看到许多回路都处于手动状态,原因是很难让过程在“自动”模式下平稳工作。 由于这些不足,采用PID的工业控制系统总是受产品质量、安全、产量和能源浪费等问题的困扰。 PID参数自整定就是为了处理PID参数整定这个问题而产生的。 现在,自动整定或自身整定的PID控制器已是商业单回路控制器和分散控制系统的一个标准。 在一些情况下针对特定的系统设计的PID控制器控制得很好,但它们仍存在一些问题需要解决:如果自整定要以模型为基础,为了PID参数的重新整定在线寻找和保持好过程模型是较难的。 闭环工作时,要求在过程中插入一个测试信号。 这个方法会引起扰动,所以基于模型的PID参数自整定在工业应用不是太好。 如果自整定是基于控制律的,经常难以把由负载干扰引起的影响和过程动态特性变化引起的影响区分开来,因此受到干扰的影响控制器会产生超调,产生一个不必要的自适应转换。 另外,由于基于控制律的系统没有成熟的稳定性分析方法,参数整定可靠与否存在很多问题。 因此,许多自身整定参数的PID控制器经常工作在自动整定模式而不是连续的自身整定模式。 自动整定通常是指根据开环状态确定的简单过程模型自动计算PID参数。 PID在控制非线性、时变、耦合及参数和结构不确定的复杂过程时,工作地不是太好。 最重要的是,如果PID控制器不能控制复杂过程,无论怎么调参数都没用。 虽然有这些缺点,PID控制器是最简单的有时却是最好的控制器[编辑本段]现实意义目前工业自动化水平已成为衡量各行各业现代化水平的一个重要标志。 同时,控制理论的发展也经历了古典控制理论、现代控制理论和智能控制理论三个阶段。 智能控制的典型实例是模糊全自动洗衣机等。 自动控制系统可分为开环控制系统和闭环控制系统。 一个控制系统包括控制器、传感器、变送器、执行机构、输入输出接口。 控制器的输出经过输出接口、执行机构,加到被控系统上;控制系统的被控量,经过传感器,变送器,通过输入接口送到控制器。 不同的控制系统,其传感器、变送器、执行机构是不一样的。 比如压力控制系统要采用压力传感器。 电加热控制系统的传感器是温度传感器。 目前,PID控制及其控制器或智能PID控制器(仪表)已经很多,产品已在工程实际中得到了广泛的应用,有各种各样的PID控制器产品,各大公司均开发了具有PID参数自整定功能的智能调节器 (intelligent regulator),其中PID控制器参数的自动调整是通过智能化调整或自校正、自适应算法来实现。 有利用PID控制实现的压力、温度、流量、液位控制器,能实现PID控制功能的可编程控制器(PLC),还有可实现PID控制的PC系统等等。 可编程控制器(PLC) 是利用其闭环控制模块来实现PID控制,而可编程控制器(PLC)可以直接与ControlNet相连,如Rockwell的PLC-5等。 还有可以实现 PID控制功能的控制器,如Rockwell 的Logix产品系列,它可以直接与ControlNet相连,利用网络来实现其远程控制功能。 1、开环控制系统开环控制系统(open-loop control system)是指被控对象的输出(被控制量)对控制器(controller)的输出没有影响。 在这种控制系统中,不依赖将被控量反送回来以形成任何闭环回路。 2、闭环控制系统闭环控制系统(closed-loop control system)的特点是系统被控对象的输出(被控制量)会反送回来影响控制器的输出,形成一个或多个闭环。 闭环控制系统有正反馈和负反馈,若反馈信号与系统给定值信号相反,则称为负反馈( Negative Feedback),若极性相同,则称为正反馈,一般闭环控制系统均采用负反馈,又称负反馈控制系统。 闭环控制系统的例子很多。 比如人就是一个具有负反馈的闭环控制系统,眼睛便是传感器,充当反馈,人体系统能通过不断的修正最后作出各种正确的动作。 如果没有眼睛,就没有了反馈回路,也就成了一个开环控制系统。 另例,当一台真正的全自动洗衣机具有能连续检查衣物是否洗净,并在洗净之后能自动切断电源,它就是一个闭环控制系统。 3、阶跃响应阶跃响应是指将一个阶跃输入(step function)加到系统上时,系统的输出。 稳态误差是指系统的响应进入稳态后,系统的期望输出与实际输出之差。 控制系统的性能可以用稳、准、快三个字来描述。 稳是指系统的稳定性(stability),一个系统要能正常工作,首先必须是稳定的,从阶跃响应上看应该是收敛的;准是指控制系统的准确性、控制精度,通常用稳态误差来(Steady-state error)描述,它表示系统输出稳态值与期望值之差;快是指控制系统响应的快速性,通常用上升时间来定量描述。 4、PID控制的原理和特点在工程实际中,应用最为广泛的调节器控制规律为比例、积分、微分控制,简称PID控制,又称PID调节。 PID控制器问世至今已有近70年历史,它以其结构简单、稳定性好、工作可靠、调整方便而成为工业控制的主要技术之一。 当被控对象的结构和参数不能完全掌握,或得不到精确的数学模型时,控制理论的其它技术难以采用时,系统控制器的结构和参数必须依靠经验和现场调试来确定,这时应用PID控制技术最为方便。 即当我们不完全了解一个系统和被控对象,或不能通过有效的测量手段来获得系统参数时,最适合用PID控制技术。 PID控制,实际中也有PI和PD控制。 PID控制器就是根据系统的误差,利用比例、积分、微分计算出控制量进行控制的。 比例(P)控制比例控制是一种最简单的控制方式。 其控制器的输出与输入误差信号成比例关系。 当仅有比例控制时系统输出存在稳态误差(Steady-state error)。 积分(I)控制在积分控制中,控制器的输出与输入误差信号的积分成正比关系。 对一个自动控制系统,如果在进入稳态后存在稳态误差,则称这个控制系统是有稳态误差的或简称有差系统(System with Steady-state Error)。 为了消除稳态误差,在控制器中必须引入“积分项”。 积分项对误差取决于时间的积分,随着时间的增加,积分项会增大。 这样,即便误差很小,积分项也会随着时间的增加而加大,它推动控制器的输出增大使稳态误差进一步减小,直到等于零。 因此,比例+积分(PI)控制器,可以使系统在进入稳态后无稳态误差。 微分(D)控制在微分控制中,控制器的输出与输入误差信号的微分(即误差的变化率)成正比关系。 自动控制系统在克服误差的调节过程中可能会出现振荡甚至失稳。 其原因是由于存在有较大惯性组件(环节)或有滞后(delay)组件,具有抑制误差的作用,其变化总是落后于误差的变化。 解决的办法是使抑制误差的作用的变化“超前”,即在误差接近零时,抑制误差的作用就应该是零。 这就是说,在控制器中仅引入 “比例”项往往是不够的,比例项的作用仅是放大误差的幅值,而目前需要增加的是“微分项”,它能预测误差变化的趋势,这样,具有比例+微分的控制器,就能够提前使抑制误差的控制作用等于零,甚至为负值,从而避免了被控量的严重超调。 所以对有较大惯性或滞后的被控对象,比例+微分(PD)控制器能改善系统在调节过程中的动态特性。 5、PID控制器的参数整定PID控制器的参数整定是控制系统设计的核心内容。 它是根据被控过程的特性确定PID控制器的比例系数、积分时间和微分时间的大小。 PID控制器参数整定的方法很多,概括起来有两大类:一是理论计算整定法。 它主要是依据系统的数学模型,经过理论计算确定控制器参数。 这种方法所得到的计算数据未必可以直接用,还必须通过工程实际进行调整和修改。 二是工程整定方法,它主要依赖工程经验,直接在控制系统的试验中进行,且方法简单、易于掌握,在工程实际中被广泛采用。 PID控制器参数的工程整定方法,主要有临界比例法、反应曲线法和衰减法。 三种方法各有其特点,其共同点都是通过试验,然后按照工程经验公式对控制器参数进行整定。 但无论采用哪一种方法所得到的控制器参数,都需要在实际运行中进行最后调整与完善。 现在一般采用的是临界比例法。 利用该方法进行 PID控制器参数的整定步骤如下:(1)首先预选择一个足够短的采样周期让系统工作;(2)仅加入比例控制环节,直到系统对输入的阶跃响应出现临界振荡,记下这时的比例放大系数和临界振荡周期;(3)在一定的控制度下通过公式计算得到PID控制器的参数。 在实际调试中,只能先大致设定一个经验值,然后根据调节效果修改。 对于温度系统:P(%)20--60,I(分)3--10,D(分)0.5--3对于流量系统:P(%)40--100,I(分)0.1--1对于压力系统:P(%)30--70,I(分)0.4--3对于液位系统:P(%)20--80,I(分)1--5参数整定找最佳,从小到大顺序查先是比例后积分,最后再把微分加曲线振荡很频繁,比例度盘要放大曲线漂浮绕大湾,比例度盘往小扳曲线偏离回复慢,积分时间往下降曲线波动周期长,积分时间再加长曲线振荡频率快,先把微分降下来动差大来波动慢。 微分时间应加长理想曲线两个波,前高后低4比1一看二调多分析,调节质量不会低[编辑本段]PID控制实现1 . PID 的反馈逻辑 各种变频器的反馈逻辑称谓各不相同,甚至有类似的称谓而含义相反的情形。 系统设计时应以所选用变频器的说明书介绍为准。 所谓反馈逻辑,是指被控物理量经传感器检测到的反馈信号对变频器输出频率的控制极性。 例如中央空调系统中,用回水温度控制调节变频器的输出频率和水泵电机的转速。 冬天制热时,如果回水温度偏低,反馈信号减小,说明房间温度低,要求提高变频器输出频率和电机转速,加大热水的流量;而夏天制冷时,如果回水温度偏低,反馈信号减小,说明房间温度过低,可以降低变频器的输出频率和电机转速.减少冷水的流量。 由上可见,同样是温度偏低,反馈信号减小,但要求变频器的频率变化方向却是相反的。 这就是引入反馈逻辑的原由。 几种变频器反馈逻辑的功能选择见表 1 。 2 .打开 PID 功能 要实现闭环的 PID 控制功能,首先应将 PID 功能预置为有效。 具体方法有两种:一是通过变频器的功能参数码预置,例如,康沃 CVF-G2 系列变频器,将参数 H-48 设为 O 时,则无 PID 功能;设为 1 时为普通 PID 控制;设为 2 时为恒压供水 PID 。 二是由变频器的外接多功能端子的状态决定。 例如安川 CIMR-G 7A 系列变频器,如图 1 所示,在多功能输入端子 Sl-S10 中任选一个,将功能码 H1-01 ~ H1-10( 与端子 S1-S10 相对应 ) 预置为 19 ,则该端子即具有决定 PI[) 控制是否有效的功能,该端子与公共端子 SC “ ON ”时无效,“ OFF ”时有效。 应注意的是.大部分变频器兼有上述两种预置方式,但有少数品牌的变频器只有其中的一种方式。 在一些控制要求不十分严格的系统中,有时仅使用 PI 控制功能、不启动 D 功能就能满足需要,这样的系统调试过程比较简单。 3 .目标信号与反馈信号 欲使变频系统中的某一个物理量稳定在预期的目标值上,变频器的 PID 功能电路将反馈信号与目标信号不断地进行比较,并根据比较结果来实时地调整输出频率和电动机的转速。 所以,变频器的 PID 控制至少需要两种控制信号:目标信号和反馈信号。 这里所说的目标信号是某物理量预期稳定值所对应的电信号,亦称目标值或给定值;而该物理量通过传感器测量到的实际值对应的电信号称为反馈信号,亦称反馈量或当前值。 PID 控制的功能示意图见图 2 。 图中有一个 PID 开关。 可通过变频器的功能参数设置使 PID 功能有效或无效。 PID 功能有效时,由 PID 电路决定运行频率; PID 功能无效时,由频率设定信号决定运行频率。 PID 开关、动作选择开关和反馈信号切换开关均由功能参数的设置决定其工作状态。 4 .目标值给定 如何将目标值 ( 目标信号 ) 的命令信息传送给变频器,各种变频器选择了不同的方法,而归结起来大体上有如下两种方案:一是自动转换法,即变频器预置 PID 功能有效时,其开环运行时的频率给定功能自动转为目标值给定.如表 2 中的安川 CIMR-G 7A 与富士 P11S 变频器。 二是通道选择法,如表 2 中的康沃 CVF-G2 、森兰 SB12 和普传 P 系列变频器。 以上介绍了目标信号的输入通道,接着要确定目标值的大小。 由于目标信号和反馈信号通常不是同一种物理量。 难以进行直接比较,所以,大多数变频器的目标信号都用传感器量程的百分数来表示。 例如,某储气罐的空气压力要求稳定在 1 . 2MPa ,压力传感器的量程为 2MPa ,则与 1 . 2MPa 对应的百分数为 60 %,目标值就是 60 %。 而有的变频器的参数列表中,有与传感器量程上下限值对应的参数,例如富士 P11S 变频器,将参数 E40( 显示系数 A) 设为 2 ,即压力传感器的量程上限 2MPa :参数 E41( 显示系数 B) 设为 0 ,即量程下限为 0 ,则目标值为 1 . 2 。 即压力稳定值为 1 . 2 MPa 。 目标值即是预期稳定值的绝对值。 5 .反馈信号的连接 各种变频器都有若干个频率给定输入端,在这些输入端子中,如果已经确定一个为目标信号的输入通道,则其他输入端子均可作为反馈信号的输入端。 可通过相应的功能参数码选择其中的一个使用。 比较典型的几种变频器反馈信号通道选择见表 3 。 6 . P 、 I 、 D 参数的预置与调整 (1) 比例增益 P 变频器的 PID 功能是利用目标信号和反馈信号的差值来调节输出频率的,一方面,我们希望目标信号和反馈信号无限接近,即差值很小,从而满足调节的精度:另一方面,我们又希望调节信号具有一定的幅度,以保证调节的灵敏度。 解决这一矛盾的方法就是事先将差值信号进行放大。 比例增益 P 就是用来设置差值信号的放大系数的。 任何一种变频器的参数 P 都给出一个可设置的数值范围,一般在初次调试时, P 可按中间偏大值预置.或者暂时默认出厂值,待设备运转时再按实际情况细调。 (2) 积分时间 如上所述.比例增益 P 越大,调节灵敏度越高,但由于传动系统和控制电路都有惯性,调节结果达到最佳值时不能立即停止,导致“超调”,然后反过来调整,再次超调,形成振荡。 为此引入积分环节 I ,其效果是,使经过比例增益 P 放大后的差值信号在积分时间内逐渐增大 ( 或减小 ) ,从而减缓其变化速度,防止振荡。 但积分时间 I 太长,又会当反馈信号急剧变化时,被控物理量难以迅速恢复。 因此, I 的取值与拖动系统的时间常数有关:拖动系统的时间常数较小时,积分时间应短些;拖动系统的时间常数较大时,积分时间应长些。 (3) 微分时间 D 微分时间 D 是根据差值信号变化的速率,提前给出一个相应的调节动作,从而缩短了调节时间,克服因积分时间过长而使恢复滞后的缺陷。 D 的取值也与拖动系统的时间常数有关:拖动系统的时间常数较小时,微分时间应短些;反之,拖动系统的时间常数较大时, 微分时间应长些。 (4)P 、 I 、 D 参数的调整原则 P 、 I 、 D 参数的预置是相辅相成的,运行现场应根据实际情况进行如下细调:被控物理量在目标值附近振荡,首先加大积分时间 I ,如仍有振荡,可适当减小比例增益 P 。 被控物理量在发生变化后难以恢复,首先加大比例增益 P ,如果恢复仍较缓慢,可适当减小积分时间 I ,还可加大微分时间 D 。
《人人都该懂的工程学》:需求/系统/负反馈
主要讲了两点: 科学家专注发现问题,探索 真实 世界; 发明家关注发明,总是在 创新 的路上,转化可能性; 工匠是把复杂的手艺 传承 给他人。 工程师是在科学理论的基础上展开工作的,站在巨人的肩膀上把科学应用到现实生活中。 相比发明家,工程师关注创新但是更加会让创新的想法落地。 和工匠精神不同的是,工匠是把普通人变成手艺人,而工程师是让普通人自己就能够简单的学会操作使用。 工程师总是把超级复杂的过程留给自己,把简洁大方的界面留给大众。 A.需求 从书中我能听得到的信息是,工程师是能够把普通人脑海中模糊状态东西的语言转化成工程师自己的专业语言。 这个需要强大的沟通转换能力,只有了解工程师上一级的真实需求,才能按照需求往下继续走。 这个是工程师能力展现的核心,我认为不仅仅是工程师,也是我们大多数人都应该掌握一个必备的技能。 用沟通的技能来挖掘到对方的真实需求,从而更好的展开工作,提高效率,节省时间! B.系统 做工控的人都知道,如果在研发的设备上多加一个零件,就意味着以后会多一个故障点。 因为多一个东西,自然就会对其他东西造成影响。 工程师要在各个零部件中进行调和,让他们之间相互影响的效果变小,尽量达到和谐统一的正常运行状态。 C.负反馈 负反馈不是负面消极的反馈,而是工程师的一种创新方法。 打个比方,比如说要一台电气设备动起来,那么首先就要做两个大方面的核心,机械和电路相匹配,也就是机械流程和电机的相互动作。 这是小圆心模型的1.0雏形; 然后再这个基础上继续延伸,需要用到伸缩的气缸,那么还要增加气动的部分,需要空压机,电池阀。 这就是小圆心向外画圈模型的2.0雏形; 最后如果要像汽车那么动起来还需要增加发动机和油路。 而链接这一个整体需要PLC程序来管理它们之间的协作运行。 让各个部分形成一个完美的整体,这就是最后形成一个大圆圈的完整3.0成品模型。 模型一直都是在反复试错,纠正,以及调整方向。 让它始终走在正确的航向上,不会偏离。 工程师一直都在根据需求优化,迭代,升级,维护产品或者服务。
本文原创来源:电气TV网,欢迎收藏本网址,收藏不迷路哦!
添加新评论