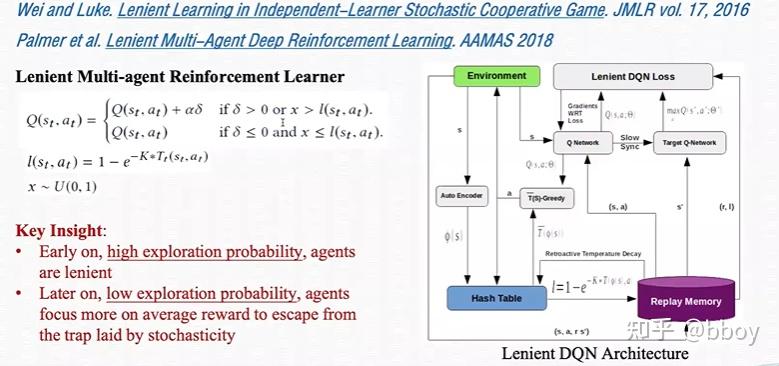
随着科技的飞速发展,智能化操作已成为现代工业制造领域不可或缺的一部分。
在众多优秀的智能化操作系统中,三菱伺服系统凭借其卓越的性能和领先的行业地位,成为业界瞩目的焦点。
本文将深入探讨三菱伺服系统的智能化操作体验,揭示其如何领先行业前沿,并阐述其所涵盖的智能化操作体系的关键要素。
一、三菱伺服系统概述
三菱伺服系统作为三菱电机旗下的重要产品,广泛应用于机床、机器人、包装机械、印刷机械等领域。
该系统具有高精度、高稳定性、高响应速度等特点,能够满足各种复杂的运动控制需求。
其先进的算法和优秀的性能,确保了精准的轨迹控制和高效率的生产过程。
二、智能化操作体验
1. 人机交互友好
三菱伺服系统采用先进的人机交互界面,操作简单直观。
用户可以通过触摸屏、电脑或其他智能设备进行实时操作和控制。
其界面设计简洁明了,功能齐全,大大降低了操作难度,提高了工作效率。
系统还具备多种语言支持,满足不同国家和地区用户的需求。
2. 自动化程度高
三菱伺服系统具备高度自动化功能,能够实现自动诊断、自动调整、自动优化等。
当系统出现故障时,能够自动进行诊断并提示用户进行维修。
在调整和优化过程中,系统可以自动进行参数调整,确保系统始终处于最佳工作状态。
3. 智能化控制策略
三菱伺服系统采用先进的控制策略,包括矢量控制、位置控制、速度控制等。
这些先进的控制策略能够确保系统的精确性和稳定性,从而实现高效的运行。
系统还支持多种控制模式,可以根据实际需求进行灵活选择。
三、领先的行业地位
1. 技术创新
三菱电机一直致力于技术研发和创新,其伺服系统在算法、硬件、软件等方面不断进行升级和改进。
这使得三菱伺服系统始终保持在行业前沿,为用户带来更好的操作体验。
2. 丰富的产品线
三菱伺服系统拥有丰富的产品线,包括交流伺服、直流伺服、线性马达等多个系列。
这些产品覆盖了从低端到高端的市场需求,满足了不同客户的不同需求。
3. 广泛的应用领域
三菱伺服系统广泛应用于机床、机器人、包装机械、印刷机械等领域。
在实际应用中,其表现出卓越的性能和稳定性,赢得了广大用户的信赖和好评。
四、智能化操作体系的关键要素
1. 智能化传感器技术
智能化传感器技术是三菱伺服系统的重要组成部分。
通过传感器,系统可以实时获取设备的运行状态和工作环境信息,从而实现精准的控制和高效的运行。
2. 云计算与大数据技术
云计算和大数据技术为三菱伺服系统的智能化操作提供了强大的支持。
通过云计算和大数据技术,系统可以实现对大量数据的处理和分析,从而优化运行过程,提高生产效率。
3. 人工智能算法
人工智能算法是三菱伺服系统实现智能化操作的核心。
通过人工智能算法,系统可以自主学习和优化,不断提高自身的性能和质量。
五、结论
三菱伺服系统凭借其友好的人机交互、高度的自动化、先进的控制策略等技术优势,在智能化操作领域处于行业前沿。
其丰富的产品线、广泛的应用领域以及强大的技术支持,使其能够满足不同客户的需求。
未来,随着技术的不断发展,三菱伺服系统将继续引领行业前沿,为用户带来更好的操作体验。
三菱伺服驱动器参数都设置什么啊 详细点 谢谢
伺服驱动器(servo drives)又称为伺服控制器、伺服放大器,是用来控制伺服电机的一种控制器,其作用类似于变频器作用于普通交流马达,属于伺服系统的一部分,主要应用于高精度的定位系统。 一般是通过位置、速度和力矩三种方式对伺服马达进行控制,实现高精度的传动系统定位,目前是传动技术的高端产品。
伺服进给系统的要求:
1、调速范围宽
2、定位精度高
3、有足够的传动刚性和高的速度稳定性。
4、快速响应,无超调。 为了保证生产率和加工质量,除了要求有较高的定位精度外,还要求有良好的快速响应特性,即要求跟踪指令信号的响应要快,因为数控系统在启动、制动时,要求加、减加速度足够大,缩短进给系统的过渡过程时间,减小轮廓过渡误差。
5、低速大转矩,过载能力强。 一般来说,伺服驱动器具有数分钟甚至半小时内1.5倍以上的过载能力,在短时间内可以过载4~6倍而不损坏。
6、可靠性高。 要求数控机床的进给驱动系统可靠性高、工作稳定性好,具有较强的温度、湿度、振动等环境适应能力和很强的抗干扰的能力。
软件基本设置:⑴双击 SETUP154C图标——设置——系统设定——机种选择“MR——E——A”;——波特率选择“9600”——串口选择“COM3这是看你自己的计算机口了”—— 有站号——确定。
⑵点站号设定:选00站。
⑶点击参数——进行“参数设定、调整、变更清单显示、详细信息显示”里——点击“参数设定”——参数一览表“批量读取、核对、批量写入、变更清单、详细信息、初期设定、终止”。
⑷参数写入操作步骤:修改表里相应参数值后——回车——点“写入”。 注意:有*好的参数伺服要停电后5S再启。
软件调试运行功能(点动运行、定位运行、无电机运行、程序运行):⑴试运行:①点动运行操作:试运行——点动运行——电机转速3000r/min注意设定时不要超过3000转——加减速时间常数1000ms——点正转停止或反转停止即可。
②定位运行操作:试运行——定位运行——电机转速200r/min注意设定时不要超过3000转——加减速时间常数1000ms——移动量pules——点正转停止或反转停止即可。
③程序运行操作:试运行——程序运行——点“编辑”——在“程序运行”里点“编辑”——出现“程序运行—编辑”栏,在右边大空白栏里输入以下程序如下:TIMS(3):运行程序3次;SPN(1000):进给转速1000r/min;STC(500):伺服到达额定转速时间500ms;MOV():正转给移动脉冲距离PULES;TIM(3) :等待下一步操作时间3秒;SPN(1000): 进给转速1000r/min;STC(500) :伺服到达额定转速时间500ms;MOV(-) :正转给移动脉冲距离PULES;STOP:停止;按“确定”——反悔程序运行界面——点“启动”这时电机按你编制的程序要求运行。
三菱mr-j4-70a伺服rle6.1伺服报警如何解决
原因是主回路断。
此时检查主回路电源是否接入,若正常则主模块检测回路故障,须更换驱动器或配件。 故障发生在操作过程中,相应的报警或显示警告采取适当的行动。
工作原理
目前主流的伺服驱动器均采用数字信号处理器(DSP)作为控制核心,
可以实现比较复杂的控制算法,实现数字化、网络化和智能化。 功率器件普遍采用以智能功率模块(IPM)为核心设计的驱动电路,IPM内部集成了驱动电路,同时具有过电压、过电流、过热、欠压等故障检测保护电路,在主回路中还加入软启动电路,以减小启动过程对驱动器的冲击。
功率驱动单元首先通过三相全桥整流电路对输入的三相电或者市电进行整流,得到相应的直流电。 经过整流好的三相电或市电,再通过三相正弦PWM电压型逆变器变频来驱动三相永磁式同步交流伺服电机。
功率驱动单元的整个过程可以简单的说就是AC-DC-AC的过程。 整流单元(AC-DC)主要的拓扑电路是三相全桥不控整流电路。
数控仿真技术论文
数控机床的发展趋势为了满足市场和科学技术发展的需要,为了达到现代制造技术对数控技术提出的更高的要求,数控未来仍然继续向开放式、基于PC的第六代方向、高速化和高精度化、智能化等方向发展。 1、开放式 为适应数控进线、联网、普及型个性化、多品种、小批量、柔性化及数控迅速发展的要求,最重要的发展趋势是体系结构的开放性,设计生产开放式的数控系统,例如美国、欧共体及日本发展开放式数控的计划等。 2、基于PC的第六代方向 基于PC所具有的开放性、低成本、软硬件资源丰富等特点,更多的数控系统生产厂家会走上这条道路。 至少采用PC机作为它的前端机,来处理人机界面、编程、联网通信等问题,由原有的系统承担数控的任务。 PC机所具有的友好的人机界面,将普及到所有的数控系统。 远程通讯,远程诊断和维修将更加普遍。 3、高速化、高效化 机床向高速化方向发展,可充分发挥现代刀具材料的性能,不但可大幅度提高加工效率、降低加工成本,而且还可提高零件的表面加工质量和精度。 超高速加工技术对制造业实现高效、优质、低成本生产有广泛的适用性。 90年代以来,随着超高速切削机理、超硬耐磨长寿命刀具材料和磨料磨具,大功率高速电主轴、高加/减速度直线电机驱动进给部件以及高性能控制系统(含监控系统)和防护装置等一系列技术领域中关键技术的解决,欧、美、日各国争相开发应用新一代高速数控机床,加快机床高速化发展步伐。 高速主轴单元(电主轴,转速-r/min)、高速且高加/减速度的进给运动部件(快移速度60~120m/min,切削进给速度高达60m/min)、高性能数控和伺服系统以及数控工具系统都出现了新的突破,达到了新的技术水平。 根据高效率、大批量生产需求和电子驱动技术的飞速发展,高速直线电机的推广应用,开发出一批高速、高效的高速响应的数控机床以满足汽车、农机等行业的需求。 还由于新产品更新换代周期加快,模具、航空、军事等工业的加工零件不但复杂而且品种增多。 4、高精度化 精密化是为了适应高新技术发展的需要,也是为了提高普通机电产品的性能、质量和可靠性,减少其装配时的工作量从而提高装配效率的需要。 从精密加工发展到超精密加工(特高精度加工),是世界各工业强国致力发展的方向。 其精度从微米级到亚微米级,乃至纳米级(<10nm),其应用范围日趋广泛。 超精密加工主要包括超精密切削(车、铣)、超精密磨削、超精密研磨抛光以及超精密特种加工(三束加工及微细电火花加工、微细电解加工和各种复合加工等)。 随着现代科学技术的发展,对超精密加工技术不断提出了新的要求。 新材料及新零件的出现,更高精度要求的提出等都需要超精密加工工艺,发展新型超精密加工机床,完善现代超精密加工技术,以适应现代科技的发展。 随着高新技术的发展和对机电产品性能与质量要求的提高,机床用户对机床加工精度的要求也越来越高。 为了满足用户的需要,近10多年来,普通级数控机床的加工精度已由±10μm提高到±5μm,精密级加工中心的加工精度则从±3~5μm,提高到±1~1.5μm。 5、高可靠性 数控系统的可靠性要高于被控设备的可靠性在一个数量级以上,但也不是可靠性越高越好,仍然是适度可靠,因为是商品,受性能价格比的约束。 对于每天工作两班的无人工厂而言,如果要求在16小时内连续正常工作,无故障率P(t)=99%以上的话,则数控机床的平均无故障运行时间MTBF就必须大于3000小时。 MTBF大于3000小时,对于由不同数量的数控机床构成的无人化工厂差别就大多了,我们只对一台数控机床而言,如主机与数控系统的失效率之比为10:1的话(数控的可靠比主机高一个数量级)。 此时数控系统的MTBF就要大于.3小时,而其中的数控装置、主轴及驱动等的MTBF就必须大于10万小时。 6、智能化 随着人工智能在计算机领域的不断渗透和发展,数控系统的智能化程度将不断提高,智能化的内容包括在数控系统中的各个方面。 (1)应用自适应控制技术 数控系统能检测过程中一些重要信息,并自动调整系统的有关参数,达到改进系统运行状态的目的。 (2)引入专家系统指导加工 将熟练工人和专家的经验,加工的一般规律和特殊规律存入系统中,以工艺参数数据库为支撑,建立具有人工智能的专家系统。 (3)引入故障诊断专家系统 (4)智能化数字伺服驱动装置 可以通过自动识别负载,而自动调整参数,使驱动系统获得最佳的运行。 可以通过自动识别负载,而自动调整参数,使驱动系统获得最佳的运行。 综上所述,由于数控机床不断采纳科学技术发展中的各种新技术,使得其功能日趋完善,数控技术在机械加工中的地位也显得越来越重要,数控机床的广泛应用是现代制造业发展的必然趋势。 国产数控机床现状及发展趋势分析时间:2008-05-04 17:07 来源: 一大把机械圈 文字选择:大 中 小20世纪80年代初,国内先后从日本、美国等国引进了一些CNC装置及主轴、伺服系统的生产技术,并陆续投入了批量生产,从而结束了数控机床发展徘徊不前的局面,推动了数控机床的发展。 到20世纪90年代初,国内的数控机床及数控系统的生产具有了一定的规模,但前进中的数控机床产业正面临十分严峻的形势。 进入WTO后,中国将进入日趋完善的国内外相统一的大市场,大量数控机床及数控系统进口,将对发展中的数控产业造成巨大的冲击。 2003年开始,中国已成为全球最大的机床消费国,也是世界上最大的数控机床进口国。 随着,“数字制造”这一新理念被引入中国制造业,有必要对国内数控机床产业的现状及趋势做些探讨。 数控机床的概念 数控机床就是在数字控制下,能在尺寸精度和几何精度两方面完成金属毛坯零件加工成所需要形状的工作母机的总称。 数控机床通常由控制系统、伺服系统、检测系统、机械传动系统及其他辅助系统组成。 国产数控机床的发展现状 一、国产数控机床与国际先进水平差距逐渐缩小 数控机床是当代机械制造业的主流装备,国产数控机床的发展经历了30年跌宕起伏,已经由成长期进入了成熟期,可提供市场1,500种数控机床,覆盖超重型机床、高精度机床、特种加工机床、锻压设备、前沿高技术机床等领域,产品种类可与日、德、意、美等国并驾齐驱。 特别是在五轴联动数控机床、数控超重型机床、立式卧式加工中心、数控车床、数控齿轮加工机床领域部分技术已经达到世界先进水平。 其中,五轴(坐标)联动数控机床是数控机床技术的制高点标志之一。 它集计算机控制、高性能伺服驱动和精密加工技术于一体,应用于复杂曲面的高效、精密、自动化加工,是发电、船舶、航天航空、模具、高精密仪器等民用工业和军工部门迫切需要的关键加工设备。 五轴联动数控机床的应用,其加工效率相当于2台三轴机床,甚至可以完全省去某些大型自动化生产线的投资,大大节约了占地空间和工作在不同制造单元之间的周转运输时间及费用。 国产五轴联动数控机床品种日趋增多,国际强手对中国限制的五轴联动加工中心、五轴铣床 onmouseover=javascript:showpos(event,this) onmouseout=javascript:ClearTimer() target=_blank>数控铣床、五轴龙门铣床、五轴落地铣镗床等均在国内研制成功,改变了国际强手对数控机床产业的垄断局面。 二、国产数控机床存在的问题 由于中国技术水平和工业基础还比较落后,数控机床的性能、水平和可*性与工业发达国家相比,差距还是很大,尤其是数控系统的控制可*性还较差,数控产业尚未真正形成。 因此加速进行数控系统的工程化、商品化攻关,尽快建成与完善数控机床和数控产业成为当前的主要任务。 目前主要问题有: 三、核心技术严重缺乏 统计数据表明,数控机床的核心技术—数控系统,由显示器、控制器伺服、伺服电机和各种开关、传感器构成,中国90%需要国外进口。 如在上海设厂的德国吉特迈集团和意大利利雅路机床集团,在烟台建厂的韩国大宇综合机械株式会社,所有的核心技术都被外方掌握。 国内能做的中、高端数控机床,更多处于组装和制造环节,普遍未掌握核心技术。 国产数控机床的关键零部件和关键技术主要依赖进口,国内真正大而强的企业并不多。 目前世界最大的3 家厂商是:日本发那客、德国西门子、日本三菱;其余还有法国扭姆、西班牙凡高等。 国内有华中数控、航天数控等。 国内的数控系统刚刚开始产业化、水平质量一般。 高档次的系统全都是进口。 华中数控近几年发展迅速,软件水平相当不错,但在电器硬件方面还需进一步提高。 目前国内一些大厂还没有采用华中数控的。 数控功能部件是另外一个薄弱环节。 某种意义上说,功能部件将构筑21世纪现代数控机床。 功能部件的性能和价格决定了数控机床的性能和价格。 功能部件不是机床附件,它是数控机床的核心代表。 国产数控机床的主要故障大多出在功能部件上,它是影响国产数控机床使用的主要根源。 从国产数控机床的开发和使用来看,功能部件急需技术攻关。 特别在数控刀具滞后现象反映相当强烈。 国产数控刀具在寿命、可*性等方面差距明显,无论在品种、性能和质量上都远远不能满足用户要求。 由于国产刀具品种少、寿命低,严重影响数控机床效率的发挥。 调研企业进口的数控机床,配用大量进口数控刀具,由于价格昂贵,用户不堪负担。 数控立、卧回转工作台,数控分度盘和数控电动刀架等数控功能部件市场中海外商家也稍胜一筹。 四、民族品牌与国际品牌差距明显 2004年6月一份广东机床用户的抽查情况透露,在数控机床的各个品牌之中,用户对欧洲、日本、美国、韩国和中国台湾等数控机床品牌的关注度已占全部市场的60%以上。 品牌知名度上的差距,导致用户在选择加工设备时把更多的机会给了海外数控机床行业的一些“实力派”。 如哈尔滨某发动机(集团)有限公司的缸体生产线是一条全自动加工线,其粗加工选用韩国大宇重工的专机自动线,精加工则选用了英国CROSS HULLE公司的专机自动线,缸盖加工线是由德国Cross. Huller公司制造的高速加工中心和专机自动线、德国产的全自动在线测量机、日本产的全自动密封检测机和清洗机组成的。 曲轴生产线为全自动柔性流水生产线,精加工线由日本的数控高速CBN 磨床、动平衡机、抛光机等组成。 机床数控系统的发展趋势从1952年第一台数控机床在美国问世,至今已有40多年的历史,计算机数控(CNC)从70年代中期出现,到现在也已有20多年了,数控技术日趋成熟。 特别是近几年来微型计算机、微电子工业及电力电子工业的迅速发展,微型计算机与CNC技术的紧密结合,使得开发和生产CNC系统的技术被越来越多的自动化装备生产厂所掌握。 因此,就当今全世界范围来说,CNC技术已经不再被少数几个国家的几个CNC系统生产厂所垄断。 到80年代末,几乎每个工业发达的国家都有了自己的数控设备生产厂,生产满足各自国家数控机床及其他机械装备所需要的数控系统。 甚至很多大型的数控机床生产厂都有自己的产品,并部分出售数控系统。 因此,CNC系统生产厂之间的竞争为激烈,数控技术的发展进入了新的阶段。 当代数控技术的发展具有下述特点:1.广泛地应用微机资源近年来被称为个人计算机(PC)的微型计算机发展很快,大规模集成电路制造技术的高速发速,使得PC的硬件结构做得很小。 主CPU的运行速度越来越高。 IPC386的主频是33MHz,IPC486、586的主频可达50~120MHz,新近Intel奔腾处理器(Pentium),主频已达450MHz。 存储器容量也很大,体积很小,由于是大批量生产,使成本下降,可靠性提高。 在软件方面,操作系统的发展,特别是Windows的应用,使得PC的操作更为简便直观。 CAD/CAM的软件大量地由小型机、工作站向PC移植,三维图显示及工艺数据库在PC上建立。 再加上PC的开放性,吸引大量技术人员投入了软件的开发,使得PC的软件资源极为丰富。 因此,更好地利用PC的软、硬件资源,就成为各国数控设备生产厂发展CNC系统十分重要的一种方法。 1992~1993年,首先是在美国及欧洲的一些小型的数控设备厂推出,例如美国的ANILAN公司推出的1100、1200、1400系列,意大利FIDIA公司的10/20/30系列,都采用了PC作为基板来开发自己的数控系统。 现在连日本FANUC、三菱公司,德国的SIEMENS公司这些以生产专用CNC设备著称的公司,也都把采用PC资源,作为其发展的一个重要方向。 他们都强调自己系统的“开放”。 日本FANUC公司把采用PC的CNC系统称之为开放型CNC系统,有150、160、180及210等系列,并正发展一种将FANUC智能终端(一种与IBM PC兼容的平板式计算机)通过高速光缆与CNC装置连接的模式。 我国中国珠峰数控公司“八五”攻关成果“中华Ⅰ型(CME988)”也采用PC作为主控板,使该系统能充分利用PC的资源,跟随PC的发展而升级。 2.小型化以满足机电一体化的要求随着微电子技术的发展,大规模集成电路的集成度越来越高,体积越来越小。 数控设备厂采用超大规模集成电路并采用表面安装工艺(SMT),实现了三维立体装配,将整个CNC装置做得很小,以适应机械制造业机电一体化的要求。 日本三菱电机株式会社,最近推出的普及型CNC MELDAS 50系列及实用型CNC MELDAS 520A系列,这两个系列都采用了32位RISC微处理器,实现超小型化的CNC装置,较原来的M310及L3、L3A,体积大为减小(H168mm×W76mm×D135mm),安装面积减小了一半,功能还有所提高。 采用了超薄型显示器(9.5in的EL及10.4in的彩色LCD)。 这个系统的微小线段加工能力提升至64m/min,最大快速进给速度为240m/min,其同步攻螺纹精度较M310提高了3倍,主轴定位时间缩短了30%。 德国SIEMENS公司最新推出的SINUMERIK 840D主控组件选用386DX或486DX,具有1~4个通道,可实现直线及圆弧插补、螺旋线插补、5轴螺旋线插补及样条插补、圆柱插补等,共可控制32个轴,并有多种校正及补偿功能,体积仅为50mm×316mm×207mm。 3.改善人机接口,方便用户使用为了使操作者能很容易地掌握数控机床的操作,数控设备生产厂努力地改善人机接口,简化编程,尽量采用对话方式,使用户使用方便,如西班牙FAGOR公司生产的FAGOR 8050系列,采用交互式编辑程序指导系统,简化程序的编辑,用简要的表格编辑程序,利用蓝图建立程序。 其8050TC型数控系统,被称为高档傻瓜式数控系统(FAGOR800系列CNC系统),其操作面板使用了符号键,用户可以根据所需加工零件,选择加工程序,输入图形数据后,即可实现半自动或全自动加工。 如果面板上的各种自动操作都没有被选上,则该CNC系统只显示坐标轴的位置值和主轴转速,操作者可以用摇柄或电子手轮对机床的各个轴进行手动操作,使用极为方便。 4.提高数控系统产品的成套性数控系统包括CNC装置、主轴及进给伺服驱动装置,以及主轴电动机、进给电动机和与其相关的检测反馈元件。 一个数控系统性能的好坏是与上述各个环节的性能密切相关的。 为了满足机床用户厂的需要,数控设备生产厂都非常重视数控产品的成套性,使系统的各个环节都能很好地匹配,使用户获得最好的使用效果。 例如,日本FANUC公司开发了经济型的O-TD、O-MD CNC装置,与之相适应也开发了经济型的αC系列的效流伺服电动机及控制系统。 日本大隈(OKUMA)公司,是一个传统的机床厂,现在也开发、生产并销售数控系统,作为一个机床厂生产数控系统,所以更重视机电一体化及产品成套性。 该公司生产数控系统在软件上更结合机械加工的工艺要求,硬件上还自行开发了绝对位置编码器、无刷伺服电动机、交流主轴电动机、光栅尺等元件,同时还提供机床控制面板及控制柜、自动编程装置,为用户提供交钥匙工程。 5.研究开发智能型数控系统所谓智能型的数控系统,早在80年代初期已经开始研究。 当时FANUC公司推出的FS15系列,就称之为AI(人工智能)CNC系统,主要是在故障诊断方面采用了专家系统。 系统利用所谓的推理软件,根据存储在系统中的知识库的经验,分析及查找故障原因。 最近FANUC公司又在开展被称为面向21世纪的课题—IMS(Intelligent Manufacturing Systems),将无缝地(Seamless)把世界范围熟练工人的技术窍门(Know how)组合进行生产系统中去。 随着工业技术发展,要求制造过程更快、更容易,以适应生产需要,一种被称为智能闭环加工(Intelligent Closed-Loop Processes ICLP)技术被采用。 这种技术是利用传感器获得适时的信息,以增强制造者取得最佳产品的能力。 图1就是智能闭环加工模型。 图1 智能闭环加工模型6.根据市场需要,开发适销对路的数控产品高新技术是数控系统发展的一个方向,另一方面开发适销对路的数控产品也是适应市场发展的需要。 我国是发展中国家,经济型数控系统在我国有着广阔的市场。 因此,开发性能优良、价钱便宜的数控系统,满足我国市场需要是很有意义的。 目前,我国的经济型数控机床每年需要量约为8000~台。 虽然有几十个厂家在生产,价格也很便宜,但是多年来技术发展不快,性能及可靠性方面还存在一些问题,不能满足市场的需求。 德国SIEMENS公司在我国建立的合资企业—西门子数控(南京)有限公司,在1997年推出了SINUMERIK 802S。 这种系统除采用G代码编程外,还有图形循环支持功能,通过软件键来进行转换。 采用15.24cm(6in)彩色液晶显示,并采用两台步进电动机作为驱动单元,驱动力矩为3.5~12N.m,价格在3万元左右。 这是西门子公司为占领中国市场所做的努力。 7.开发新的数控产品随着机械加工技术的发展,对数控机床的性能要求越来越高,迫切地需要开发一些新的机电一体化数控产品来适应及满足这些要求。 例如,铝合金材料的大量采用,要求进行高速切削,以实现高的精度及低的表面粗糙度的要求,数控车床及加工中心主轴转速要求提高到~r/min,这对采用传统的机械传动是很难实现的。 因此,将电动机的电枢直接与机床的主轴做成一体的“电动主轴”,就成为生产中急需的产品。 目前,日本的FANUC公司、NSK公司,瑞士的IBAG公司,意大利的GANFIOR公司都在开发生产这种新产品。 同样,为了实现高速移动,要求开发“直线电动机”,用以直接带动工作台直线运动。 日本FANUC公司生产的直线电动机,移动速度可以达到100m/min。 日本的THK公司,德国的INDRAMAT公司、SIEMENS公司都在开发及生产这类产品。 综上所述,数控技术的发展是与现代计算机技术、电子技术发展同步的,同时也是根据生产发展的需要而发展的。 现在数控技术已经成熟,发展将更深更广更快。 未来的CNC系统将会使机械更好用,更便宜
本文原创来源:电气TV网,欢迎收藏本网址,收藏不迷路哦!
添加新评论