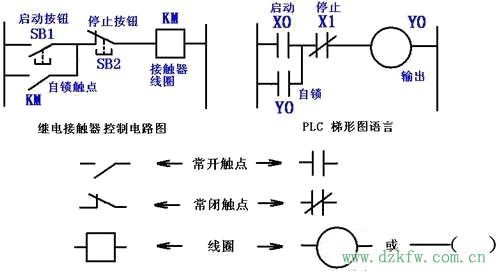
一、引言
在现代工业控制系统中,可编程逻辑控制器(PLC)作为核心组件,广泛应用于各种生产场景。
PLC初始设置是确保PLC正常运行的关键环节,其设置的好坏直接影响到整个控制系统的稳定性和性能。
本文将详细介绍PLC初始设置的重要性、设置步骤及其应用场景。
二、PLC初始设置的重要性
1. 确保系统稳定性:PLC初始设置包括参数配置、地址分配、输入输出设定等,这些设置的正确与否直接关系到控制系统的稳定性。如果设置不当,可能导致系统运行时出现错误、故障或性能下降。
2. 提高生产效率:合理的PLC初始设置能够优化生产流程,提高生产效率。通过精确配置PLC参数,可以实现生产过程的自动化、智能化,降低人工干预,提高生产质量。
3. 降低维护成本:在PLC初始设置阶段,对硬件和软件进行合理配置,可以延长设备使用寿命,减少故障率,降低维护成本。
4. 便于故障诊断与排查:正确的PLC初始设置有助于故障诊断与排查。在发生问题时,可以通过查看初始设置参数,快速定位问题所在,缩短故障处理时间。
三、PLC初始设置的步骤
1. 硬件连接与配置:根据实际需求,连接PLC与现场设备,如传感器、执行器等。确保接线正确、牢固。
2. 参数设置:根据设备规格和生产需求,设置PLC的各项参数,如采样周期、控制周期、输入输出范围等。
3. 地址分配与配置:为PLC的输入输出端口分配地址,确保与其他设备通信正常。
4. 编程与测试:根据生产工艺要求,编写控制程序,并进行测试,确保程序功能正常。
5. 调试与优化:在实际运行环境中进行调试,根据运行结果对PLC参数进行优化,提高系统性能。
四、PLC应用场景及初始设置要点
1. 自动化生产线:在自动化生产线中,PLC负责控制各种生产设备,实现生产过程的自动化。初始设置时,需根据生产线的具体要求,合理配置输入输出端口、采样周期、控制周期等参数,确保生产线的稳定运行。
2. 机器人控制:在机器人控制系统中,PLC作为核心控制器,负责接收指令并控制机器人执行动作。初始设置时,需根据机器人的运动轨迹、速度、力度等要求,精确配置PLC参数,实现机器人的精确控制。
3. 数控系统:在数控机床等数控系统中,PLC负责控制机床的运转、加工过程等。初始设置时,需根据机床的型号、加工要求等,合理设置PLC参数,确保机床的精确运行和加工质量。
4. 监控系统:在监控系统中,PLC负责数据采集、处理与传输。初始设置时,需合理配置输入输出端口、通信协议等,确保数据的准确采集和实时传输。
五、如何优化PLC初始设置以提高系统性能
1. 充分了解实际需求:在进行PLC初始设置前,充分了解生产工艺、设备性能等实际需求,确保设置的合理性。
2. 选择合适的PLC型号:根据实际需求选择合适的PLC型号,确保其满足生产需求并具有一定的余量。
3. 遵循规范操作:在进行PLC初始设置时,遵循规范操作,确保设置的正确性。
4. 实时优化调整:在实际运行过程中,根据生产情况实时优化调整PLC参数,提高系统性能。
六、结论
PLC初始设置是确保PLC正常运行的关键环节,其设置的合理性直接影响到整个控制系统的稳定性和性能。
因此,在进行PLC初始设置时,需充分了解实际需求、选择合适的PLC型号、遵循规范操作、实时优化调整,以确保PLC控制系统的稳定运行和提高生产效率。
本文原创来源:电气TV网,欢迎收藏本网址,收藏不迷路哦!
添加新评论