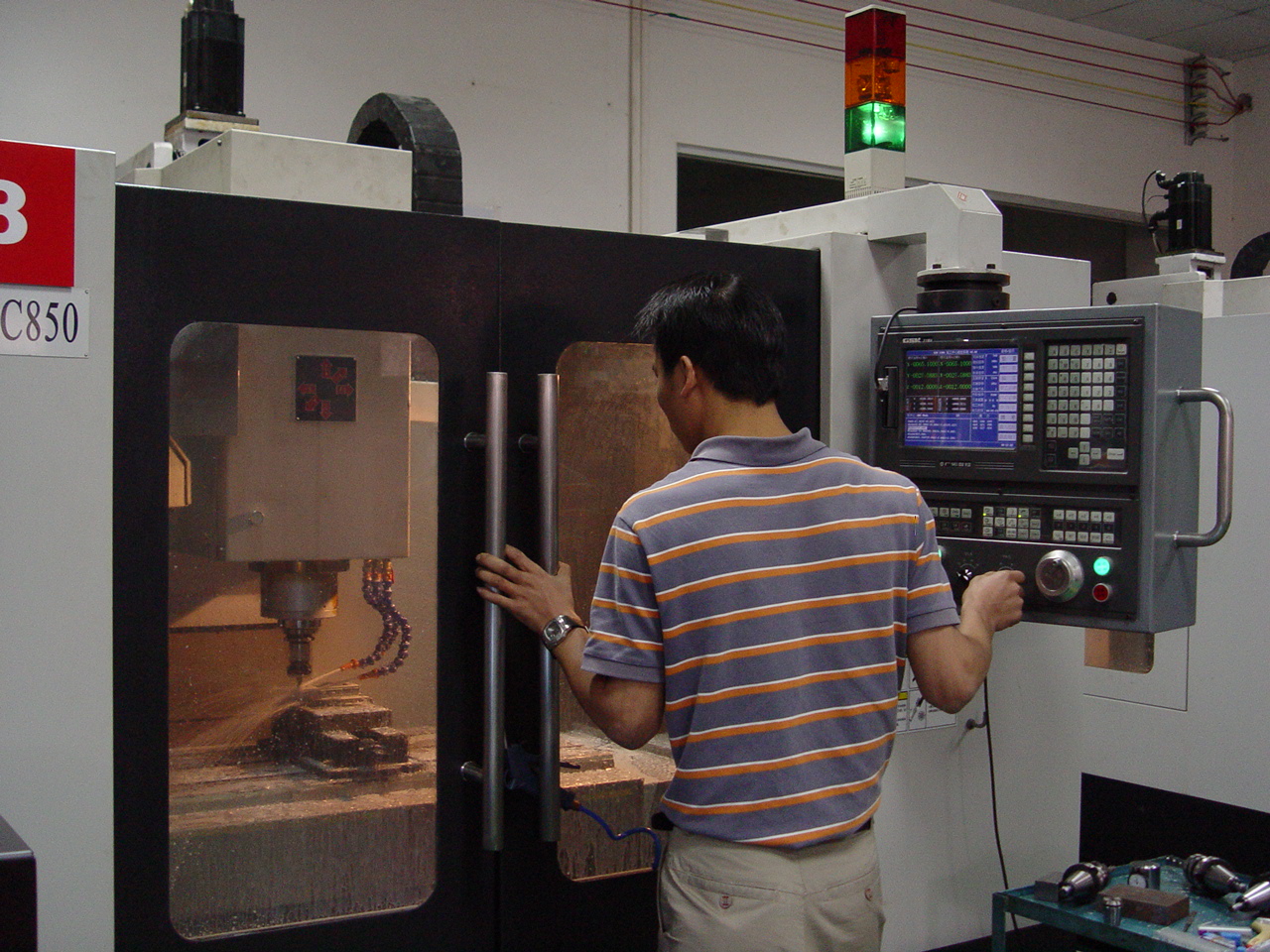
一、引言
随着工业自动化的快速发展,机床操作与PLC(可编程逻辑控制器)控制程序的协同工作已成为现代制造业的核心技术之一。
PLC控制程序在机床操作中发挥着关键作用,通过精确控制机床的运行,实现高效、精确的加工。
本文将详细介绍机床操作与PLC控制程序协同工作的原理、过程及注意事项。
二、机床操作概述
机床是制造业中用于加工各种材料的基础设备,包括车床、铣床、磨床等。
机床操作主要涉及对机床进行手动或自动操作,以实现所需的加工任务。
在操作机床时,需严格遵守安全规范,确保人员和设备的安全。
三、PLC控制程序在机床中的应用
PLC作为一种数字计算机控制系统,广泛应用于机床自动化领域。
PLC控制程序通过接收输入信号,执行一系列逻辑运算和决策,然后输出控制信号,以驱动机床执行各种动作。
在机床操作中,PLC控制程序的主要功能包括:
1. 控制机床的启动、停止和运行状态。
2. 监控机床的运行过程,确保加工过程的精确性和稳定性。
3. 根据加工需求调整机床的运行参数,如速度、位置等。
4. 实现对机床故障的诊断和报警。
四、机床操作与PLC控制程序的协同工作原理
机床操作与PLC控制程序的协同工作主要依赖于人机界面(HMI)和PLC之间的通信。
操作者通过HMI向PLC发送指令,PLC接收指令后,根据预先编写的程序对机床进行精确控制。
具体过程如下:
1. 操作者通过HMI选择加工任务,输入相关参数(如加工材料、加工路径等)。
2. HMI将指令和参数传递给PLC。
3. PLC根据接收到的指令和参数,控制机床的各个运动轴和辅助装置(如夹具、刀具等)进行协同工作。
4. PLC在控制机床的同时,不断接收机床的反馈信号,如温度、压力、位置等,以确保加工过程的精确性和稳定性。
5. 若在加工过程中出现异常情况,PLC会及时发出警报,并通过HMI显示相关信息,以便操作者进行调整或处理。
五、协同工作的注意事项
1. 安全操作:在操作机床时,必须严格遵守安全规范,确保人员和设备的安全。操作者应接受专业培训,熟悉机床和PLC控制系统的操作。
2. 程序调试:在协同工作之前,需要对PLC控制程序进行调试,确保其能够准确控制机床的运行。
3. 参数设置:根据加工需求,合理设置PLC控制程序的参数,以保证加工过程的精确性和稳定性。
4. 故障诊断:在协同工作过程中,要密切关注机床和PLC控制系统的运行状态,一旦发现异常,应及时进行诊断和排除。
5. 维护保养:定期对机床和PLC控制系统进行维护保养,以延长其使用寿命。
六、结论
机床操作与PLC控制程序的协同工作是现代制造业中的关键技术之一。
通过深入了解机床操作和PLC控制系统的原理及应用,操作者可以更加熟练地掌握这一技术,提高机床的自动化水平,实现高效、精确的加工。
同时,在协同工作过程中,需要注意安全操作、程序调试、参数设置、故障诊断和维护保养等方面的问题,以确保协同工作的顺利进行。
本文原创来源:电气TV网,欢迎收藏本网址,收藏不迷路哦!
添加新评论