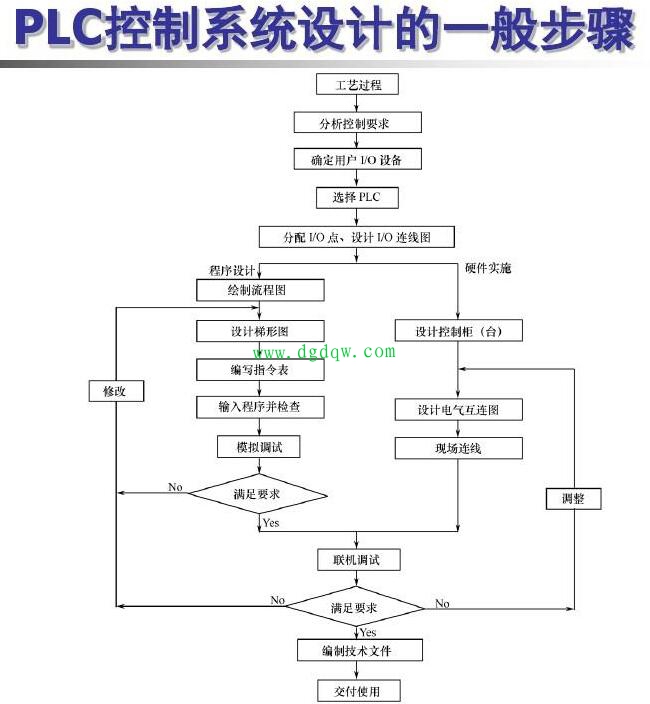
一、引言
随着工业自动化技术的快速发展,PLC(可编程逻辑控制器)系统已广泛应用于各类生产场景中。
PLC系统作为工业自动化的核心设备,其稳定性和安全性对生产过程的连续性和效率具有重要影响。
为了确保PLC系统的安全及应对潜在的威胁,自我销毁机制作为一种特殊的安全措施逐渐受到关注。
本文将探讨PLC自动化系统中的自我销毁机制,分析其工作原理、应用场景,并探讨其面临的挑战与未来发展。
二、PLC自动化系统概述
PLC自动化系统是一种基于数字计算机技术的工业控制装置,用于执行一系列逻辑运算、顺序控制、定时、计数等功能,实现对工业生产过程的控制。
PLC系统主要由CPU、存储器、输入输出接口、通信接口等部分组成。
在工业自动化生产过程中,PLC系统根据预设的程序和指令,对生产设备进行自动控制,实现生产过程的自动化和智能化。
三、自我销毁机制的概念及工作原理
自我销毁机制是一种在PLC自动化系统中的特殊安全保护措施,其主要目的是在PLC系统遭受严重攻击或损坏时,通过预设的程序和指令,使系统能够自动销毁其存储的数据、程序或功能,以保护系统的安全性和数据的完整性。自我销毁机制的工作原理主要包括以下几个方面:
1. 触发条件:设定特定的触发条件,如系统遭受恶意攻击、硬件故障等,当这些条件满足时,自我销毁机制被激活。
2. 销毁过程:在自我销毁机制被激活后,系统将执行预设的销毁程序,如删除存储数据、格式化存储器、关闭关键功能等。
3. 销毁确认:销毁过程完成后,系统会通过特定的方式确认销毁操作已完成,如发送报警信号、显示销毁状态等。
四、自我销毁机制在PLC自动化系统的应用场景
在PLC自动化系统中,自我销毁机制的应用场景主要包括以下几个方面:
1. 防止数据泄露:当PLC系统遭受恶意攻击或数据泄露风险时,自我销毁机制可以自动销毁存储的数据,保护生产过程中的重要信息不被泄露。
2. 保护系统安全:当PLC系统遭受严重破坏或无法恢复时,自我销毁机制可以关闭关键功能或使整个系统失效,避免潜在的安全风险。
3. 应对硬件故障:当PLC系统的硬件设备出现故障且无法修复时,自我销毁机制可以删除与该设备相关的数据和程序,避免故障扩散到其他设备。
五、PLC自动化系统中自我销毁机制面临的挑战与未来发展
在PLC自动化系统中实现自我销毁机制面临着一些挑战,如触发条件的准确判定、销毁过程的可控性、数据的恢复与重建等。为了克服这些挑战,未来的自我销毁机制需要解决以下问题:
1. 提高触发条件的准确性:准确判定触发条件是自我销毁机制的关键,需要综合考虑多种因素,如系统安全性、运行环境等。
2. 加强销毁过程的可控性:在销毁过程中,需要确保销毁操作的准确性和可控性,避免误操作或误删除重要数据。
3. 数据恢复与重建:自我销毁机制需要考虑到数据恢复与重建的问题,以便在必要时能够恢复生产过程的正常运行。
随着物联网、云计算等技术的快速发展,PLC自动化系统将与这些技术更加紧密地结合,自我销毁机制也需要与时俱进,实现与其他技术的融合与发展。
例如,利用云计算技术实现远程监控和管理PLC系统的自我销毁机制,提高系统的安全性和可维护性。
六、结论
PLC自动化系统中的自我销毁机制是一种重要的安全保护措施,能够在系统遭受攻击或损坏时保护系统的安全性和数据的完整性。
虽然目前自我销毁机制还面临一些挑战,但随着技术的不断发展,相信未来会有更多的创新技术和方法来解决这些问题,使PLC自动化系统的安全性得到进一步提高。
自动化制造系统中的PLC(第三部分)
在自动化制造的精密脉络中,PLC(可编程逻辑控制器)如同中枢神经系统,驱动着生产线的高效运作。 让我们深入探讨PLC的硬件构成与关键功能,以更直观地理解这个智能设备在实际应用中的角色。 首先,PLC的核心硬件组件包括:- **强大电源**: 内置或可外接,常见的电压规格有24V DC和120V/220V AC,为整个系统提供稳定的能源支持。 - **中央处理器(CPU)**: 作为大脑,负责存储和执行复杂的梯形逻辑指令,确保精确的控制流程。 **输入与输出模块**是PLC与外部设备交互的关键桥梁:- 逻辑与连续控制的实现,就像灯泡开关,通过驱动器如电磁阀、电动机启动器或伺服电机来操作。 - 传感器如接近开关、开关、电位器和LVDT,捕捉实时数据,供PLC解析。 输入端口需要特别注意,PLC输入既可以是内置的,也可以是模块化的,电压范围广泛,如12-24Vdc和100-120Vac。 值得注意的是,一些输入卡需要额外的外部电源,如24Vac供电的开关,其与PLC的连接需确保逻辑电平的准确转换。 梯形逻辑电路是PLC运作的核心,它要求电压沿完整回路传递,公共电压(如0V)和地线(接地系统)的区分至关重要。 每个输入卡独立连接,输出则需连接公共电压,这涉及到直流安全和交流抗干扰的选择,每一步都需精确计算。 输出模块的抉择至关重要,如继电器、晶体管/三极管等,它们在电流处理和转换上各有特点。 例如,继电器适用于大功率负载,而晶体管则提供单向导通特性。 在设计中,务必确保电源独立,避免混合电源问题,如图3.5-3.7所示的连接示例。 在实际案例中,如24V液压机使用双电磁阀和220Vac/20A液压泵,控制逻辑通过按钮和极限开关进行,所有设备都采用直流供电,确保了系统的稳定性和安全性。 电气布线图清晰标明各部分,如主断路开关、保险丝和输出控制线路,如图3.9所示。 遵循国际标准,如JIC符号,停止按钮应设置为常闭,启动按钮为常开,确保操作流程的逻辑清晰,如图3.10-12所示。 PLC处理着复杂的交流与直流输入,输出设备则根据其功能选择晶体管、三极管或继电器,输入/输出地址的设定基于设备的实际位置和编号。 总之,PLC的硬件设计和操作原理是自动化制造系统中不可或缺的一部分,它通过精确的逻辑控制和灵活的接口,确保了生产线的高效运行和安全性。 深入了解这些,将有助于我们更好地掌握PLC在制造过程中的实际应用。
自动化中plc是控制系统吗
是的,PLC是自动化控制系统的重要组成部分。
PLC,即可编程逻辑控制器,是自动化控制领域中的核心设备之一。
PLC系统在自动化控制中扮演关键角色。 PLC能够接收并处理各种输入信号,根据预先设定的程序进行逻辑运算和控制,进而实现对设备的自动控制。 它可以按照设定的参数和逻辑对机械设备、工艺流程进行精准控制,确保生产过程的自动化和高效化。 PLC的出现大大提高了生产的效率和质量,减少了人为干预的需求,为工业自动化的发展做出了重要贡献。
此外,PLC系统还具有高度的灵活性和可靠性。 它可以根据不同的控制需求进行编程和配置,适应于各种复杂的生产环境和工艺流程。 PLC采用先进的电子技术和智能化设计,具有高度的抗干扰能力和稳定性,能够在恶劣的工作环境下长时间稳定运行,确保控制系统的可靠性和安全性。
总之,PLC是自动化控制系统中的核心组成部分。 它通过接收和处理输入信号,根据预设程序进行逻辑运算和控制,实现对设备的自动控制,从而提高生产效率和质量。 同时,PLC系统还具有高度的灵活性和可靠性,能够适应各种复杂的生产环境和工艺流程。
自动化制造系统中的PLC(第十四部分)
14.1 PL</C存储器:智能中枢</
PLC的核心存储器肩负着计算与决策的重任,诸如计时器和计数器等功能模块,它们收纳着丰富多样的程序和数据结构,为制造过程提供精确的指令支持。
14.2 地址的艺术:程序与数据的双面手</
PLC的存储器地址巧妙地划分为程序存储区和数据存储区,如同一个图书馆的分类系统。 例如,文件数组每个单元容纳1000个元素,最初的八个文件空间预留给系统信息、结构化功能控制(SFC)和用户自定义程序。 后续的文件则为子程序提供空间,灵活扩展。
14.3 程序与数据的篇章</
程序文件0-2分别珍藏着系统设置、SFC和用户程序的智慧,编程软件编织的梯形逻辑逻辑链,一旦生成,就固化在不可改动的程序文件中,确保运行的稳定性。
14.4 数据仓库:多样化的信息存储</
数据文件0-999,每个地址都由字母和数字编排,从浮点数到状态信息,种类繁多。 一些文件位置固定,而其他则可随需调整,显示了PLC存储的灵活性。
14.5 数据寻址的艺术:精确与灵活</
PLC的数据寻址巧妙地利用斜杠和位号,如“数据位/计数器/定时器”,直接或间接地指示内存位置,为可变程序提供了动态调整的可能。
14.6 数字世界:字寻址的魅力</
无论是整数还是浮点数,PLC都采用整数字寻址的方式,简洁而高效地处理数据运算。
14.7 直接与间接:定义数据的新维度</
PLC允许直接定义整数和实数,支持十六进制和二进制表示,同时,数组这一结构更是通过井号标识,明确位置和长度,为复杂数据管理开辟了新径。
14.8 程序的智能解读:间接寻址的魔法</
PLC处理间接地址,如“I:000/[N7:2]”,通过内存位置的变化实现动态寻址,这对于可调整的程序设计来说,无疑增加了灵活性。 但同时,表达式的实时解析需谨慎,因为它们可能在运行时才被解读。
14.9 寻址与控制的深度探索</
章节深入探讨了数据类型、表达式以及间接寻址,这些功能在早期PLC中可能尚未全面支持。 图14.11展示了配备函数的梯形逻辑,展现了一个强大而精密的控制世界。
用户位存储器与实时监控</
位存储器充当内部状态的追踪者,无论是单独访问还是以整数组的形式,都为实时监控提供了便利。 计时器和计数器存储器不仅拥有预置值,还能累加,位值读写权限明确区分,如S2位用于记录PLC工作状态。
存储器的精细控制</
例如,S2:28代表看门狗设定点,S2:29则是故障例行程序的文件号,每个地址都承载着控制流程的精髓。 通过这些存储位,PLC实现了精密的控制和状态跟踪,如扫描时间和中断设置。
本文原创来源:电气TV网,欢迎收藏本网址,收藏不迷路哦!
添加新评论