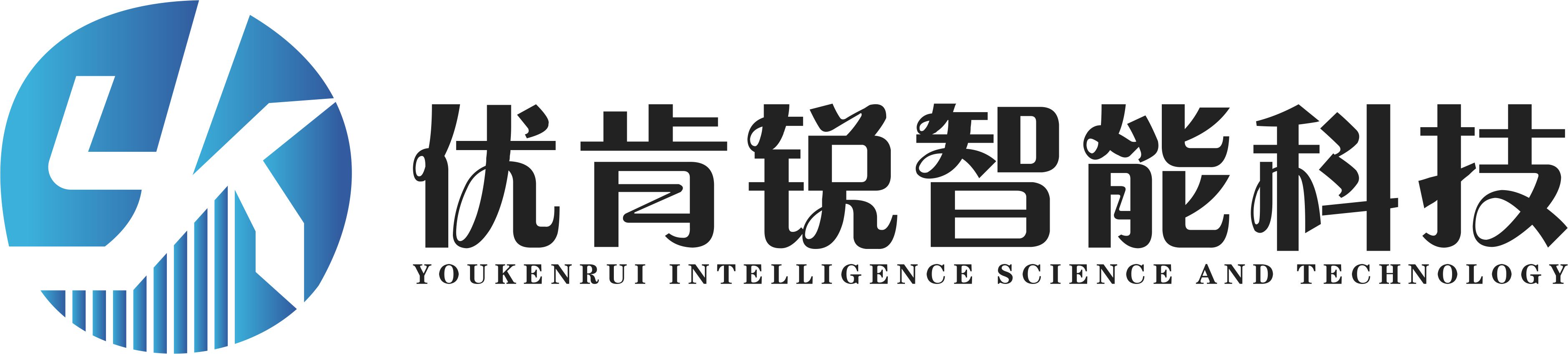
一、引言
随着工业自动化水平的不断提高,PLC(可编程逻辑控制器)在工业生产中的应用越来越广泛。
PLC作为一种数字计算机控制器,具有可靠性高、灵活性强、易于操作等特点,广泛应用于各种自动化生产系统中。
本文将探讨如何利用PLC优化工作流程并实现高效工作台位置管理。
二、PLC的基本概述
PLC,即可编程逻辑控制器,是一种专门为工业环境设计的数字计算机控制器。
它可以对工业环境中的各种信号进行采集、处理和控制,实现自动化生产。
PLC的基本功能包括逻辑控制、数据处理、通信等,广泛应用于机械制造、汽车制造、化工、食品等行业。
三、利用PLC优化工作流程
1. 自动化控制:PLC可以实现生产设备的自动化控制,减少人工操作,提高生产效率。通过预设程序,PLC可以根据生产需求自动调整设备工作状态,实现生产过程的自动化。
2. 实时监控:PLC可以实时采集生产设备的运行数据,如温度、压力、速度等,通过监控界面展示给操作人员,使操作人员可以实时了解设备的运行状态,及时发现并处理问题。
3. 故障预警:PLC可以根据设备的运行数据,通过预设的算法判断设备是否可能出现故障,提前预警,避免生产中断。
4. 数据记录与分析:PLC可以记录生产过程中的各种数据,如生产数量、设备运行时间等,通过数据分析,找出生产瓶颈,优化生产流程。
四、基于PLC实现高效工作台位置管理
1. 工作台自动化调度:通过PLC控制,可以实现工作台的自动化调度。根据生产需求,PLC可以自动调整工作台的位置,实现生产线的灵活配置。
2. 精准定位:PLC可以通过与传感器、编码器等设备的结合,实现工作台的精准定位。通过采集工作台的实时位置信息,PLC可以确保工作台准确到达指定位置,避免碰撞或错位。
3. 生产线协同作业:在多条生产线的情况下,通过PLC的集中控制,可以实现各生产线之间的协同作业。PLC可以根据生产需求,协调各生产线的工作台位置,提高生产效率。
4. 信息化管理:通过PLC与上位机的连接,可以实现工作台位置管理的信息化。操作人员可以在上位机上实时监控各工作台的位置状态,进行远程操控,提高管理效率。
五、案例分析
以某机械制造企业为例,该企业引入PLC系统后,实现了生产线的自动化控制、实时监控、故障预警和数据分析。
同时,通过PLC控制工作台的位置,实现了工作台的自动化调度、精准定位和生产线的协同作业。
引入PLC系统后,该企业的生产效率提高了30%,故障率降低了20%,取得了显著的经济效益。
六、结论
利用PLC优化工作流程并实现高效工作台位置管理具有重要的现实意义。
通过PLC的自动化控制、实时监控、故障预警、数据记录与分析等功能,可以提高生产效率,降低故障率。
同时,通过PLC控制工作台的位置,实现工作台的自动化调度、精准定位和生产线的协同作业,可以提高生产线的管理效率。
因此,企业应积极引入PLC技术,推动工业自动化的进程。
PLC自动控制系统是什么啊?
PLC自动控制系统是一种基于可编程逻辑控制器的自动化系统。
详细解释:
PLC,即可编程逻辑控制器,是现代工业自动化的核心设备之一。 PLC自动控制系统利用PLC的技术特点,通过编程实现对工业过程或机械设备的自动化控制。
1. PLC的基本功能:PLC作为控制系统的核心,能够接收并处理各种输入信号,根据预设的程序和逻辑进行运算和处理,然后输出控制信号驱动工业设备或过程。 这种处理可以是简单的开关控制,也可以是复杂的模拟量控制和数据处理。
2. 自动化控制的应用:PLC自动控制系统广泛应用于机械制造、化工、电力、环保等多个领域。 例如,在生产线中,PLC可以根据产品的检测信号自动调整机械的运行状态,实现自动化生产。 在化工过程中,PLC可以精确控制温度、压力、流量等参数,保证生产过程的稳定性和安全性。
3. 系统的特点:PLC自动控制系统具有高度的可靠性和稳定性,能够适应各种恶劣的工作环境。 同时,PLC具有强大的编程能力,可以通过改变程序来调整系统的功能,满足不同生产需求。 此外,PLC自动控制系统还具有故障诊断和自我保护功能,能够及时发现并处理系统的故障。
总结来说,PLC自动控制系统是现代工业自动化的重要组成部分,它通过PLC的技术实现工业过程或机械设备的自动化控制,提高了生产效率,降低了人工成本和操作难度。
电气控制与plc技术论文
在电气行业的实际工作中,PLC技术的加入对其发展起到了很大的促进作用,在改进完善电气系统的同时更提高了电气控制的工作质量,对电气行业今后的发展有着重大影响。 下面是我整理的电气控制与plc技术论文,希望你能从中得到感悟!
电气控制与plc技术论文篇一
电气控制与PLC技术研究
在现今高科技水平的带动下,所有技术设备都在不断的升级,对电气控制系统的要求也变得越来越高。 在电气行业的实际工作中,PLC技术的加入对其发展起到了很大的促进作用,在改进完善电气系统的同时更提高了电气控制的工作质量,对电气行业今后的发展有着重大影响。
【关键词】电气控制 PLC技术 探析
PLC从外观来讲,具有体积小质量轻的特点,小型的PLC底部尺寸一般不超过100mm,质量不超过150g,所以在安装方便,和电气系统组装容易。 PLC应用范围广泛,一般的电气控制场所都可以使用,尤其是数据应用能力在数字控制方面的运用更为广泛。 另外,抗干扰技术的应用更使电气控制系统运行的安全性和可靠性提供了有力保障。 PLC外部检测系统的设置,为自身内部和系统外部的故障检验提供了良好的条件。 而且,PLC的安装操作简单易懂,对于从事电气控制方面的人员来说掌握起来也比较容易。 储存逻辑是PLC技术在实际应用中所使用的,接线比较简单,这样也方便日后维修和改造,在减少工作量的同时又提高了工作效率。
1 PLC技术与电气控制融合后的工作流程
电气控制主要是通过对电气设备一次和二次回路控制来确保设备正常运行,其在现代工业自动化方面已经成为一个不可缺少的重要角色,更是推进工业自动化发展的重要武器。 而PLC技术的实质就是一个控制器,专门用于专业控制,主要利用计算机、通讯技术、自动化等技术发展起来的通讯控制器。 PLC技术与电气控制技术融合可以生成强大的抗干扰能力和自我诊断能力,完善电气的控制系统的同时有效排除系统中故障。
目前,PLC技术在电气控制行业的应用十分广泛,很多企业开始逐渐重视这些外来技术的引进,作为现代电控行业中的重要角色,PLC技术的应用将会在很大程度上推动电气控制行业的发展。 同时,想要PLC技术与电气控制合理融合就必须要对PLC技术有一定的掌握和了解,这是PLC技术能够更好的运用于实际的前提条件和重要基础。 此外,PLC技术在工业体系中也有着广泛应用,如石油、建材、钢铁、化工、电力、机械制造、汽车、交通运输等。
结合PLC的工作流程,根据实际工作经验,将PLC技术与电气控制融合后的工作流程划分为三个阶段。 主要有收集和输入原始数据、用户程序执行、刷新输出。
(1)采取收集数据是PLC工作进程的第一步。 通过扫描的方式依次读取并存储输入状态点和数据,同时存入I/O映像区中的相应单元。 完成后,进入用户程序执行和输出的刷新阶段。 在这一阶段,I/O映像区中相应单元的状态和数据不发生改变。
(2)在第一步完成的基础上,对用户程序按照由上到下的顺序扫描。 用户程序是执行阶段,具体的实施中,先扫描用户程序左边的控制线路,同时依然遵守由上到下和由左到右的顺序对触点构成的的控制线路进行逻辑运算。 同样,在I/O映像区内单元中的状态和数据也不会发生变化,但其他输出点和软设备在I/O映像单元区域或系统RAM存储区域的状态和数据都可能会发生变化。
(3)PLC工作流程的最后阶段,即输出刷新阶段。 在用户程序扫描结束后,PLC就会进入输出刷新阶段。 此阶段中,CPU按照I/O映像区相应的状态和数据刷新所有输出锁存电路之后再由输出电路完成相应设备的驱动设置是PLC的最后输出过程。
PLC的工作流程与大部分其他的机械设备相似,是一个周期循环的过程。 这三个工作阶段是循环运行的,每进行三个阶段为一个周期。 PLC技术与电气控制技术的融合在提高工作效率的同时又节省了故障和开发研究的开销。
2 PLC技术在电气控制应用中常见的问题
系统控制出现故障。 可能由于线路老化、周围环境破坏等原因造成控制出现故障,进而无法将信号传递给系统内部,也就无法完成对数据的接收、加载和转换,同时对系统发出的其他执行命令也没办法接收。
数据收集和传输故障也可能是由于开关一类的设备操作不到位造成的,例如打开、闭合不彻底,致使无法接收或接收错误信息,造成控制运作出现错误,系统无法正常运行,即造成了PLC无法接收信号控制系统出现故障。
设备开关和现场变送器的自身故障也是使PLC技术无法正常工作的原因,引发故障的原因可能是接线接触不良,出现破损等,同样也会造成以上PLC控制分析系统无法接收数据和进一步的处理。 此外,人为操作出错也是造成系统故障的原因之一。
3 PLC技术问题相应的解决方法
对输入PLC控制系统信号的可靠性加强注意。 保证所有的现场设备和相关部件的性能完好,杜绝由于设备自身零部件问题造成信号无法正常传送和接收的现象发生。 此外,更新改进主界面功能模块设置也有利于减少控制的出错。
完善系统设置,使其更加具有可靠性、自动化、网络一体化。 在PLC电气控制系统遭受破坏或出错时,起到预警系统的报警作用,这项功能在PLC系统控制里十分重要,能够有效的对工作情况进行监控,减少了由于指令出错带给系统的损失。 确保PLC周围的运行环境,及时排除干扰因素,实施24小时监控。
加强人员的技术培训,提高业务能力和自身素质修养,鼓励员工学习新技术、新的方法和技巧来提高工作质量。
4 总结
面对如今高科技迅猛发展的形势,在任何领域如果想要健康长远的发展,就必须不断的学习掌握新的技术,只有对新技术和设备做好充分的了解和学习并合理应用,才会真正的有所收获。 PLC在电气控制方面发挥着巨大的推动作用,二者的融合将会在很大程度上促进电气控制行业的进步发展。
参考文献
[1]牛云.先进飞机电气系统计算机控制与管理系统主处理机关键技术研究[D].西北工业大学,2006.
[2]陈实. MW级风力发电系统单机电气控制技术研究――无功补偿和偏航控制系统[D].南京航空航天大学,2004.
[3]周石强,郭强,朱涛,刘旭东.电气控制与PLC应用技术的分析研究[J].中华民居(下旬刊),2014,01:199.
[4]付焕森,李元贵.基于工程应用型人才培养的项目驱动教学与研究――以电气控制与PLC技术项目课程为例[J].大众科技,2012.
作者简介
张车(1981-),男,江苏省张家港市人。 本科学历。 中级工程师。 研究方向为电气自动化控制。
作者单位
张家港沙钢集团 江苏省张家港市
电气控制与plc技术论文篇二
电气控制与PLC技术的应用
摘 要:针对传统数控车床在自动化控制功能方面的薄弱,以CK6140普通数控车床为对象,详细探讨了数控车床的电气控制,基于PLC实现了数控车床的自动化改造功能,给出了详细的电气化、自动化改造的方案和控制结构,对于进一步提高PLC自动化控制技术在电气控制领域中的应用具有较好的借鉴意义。
关键词:电气控制;PLC技术;自动化;无人值守
1 引言
随着可编程逻辑控制器(PLC)技术的逐渐发展,很多工业生产要求实现自动化控制的功能,都采用PLC来构建自动化控制系统,尤其是对于一些电气控制较为复杂的电气设备和大型机电装备,PLC在电气化和自动化控制方面具有独到的优势,如顺序控制,可靠性高,稳定性好,易于构建网络化和远程化控制,以及实现无人值守等众多优点。 基于此,PLC技术逐渐成为工业电气自动化控制的主要应用技术。
本论文主要结合数控机床的电气化功能的改造,详细探讨数控机床电气化改造过程中基于PLC技术的应用,以及PLC技术在实现数控机床自动化控制功能上的应用,以此和广大同行分享。
2 数控机床的电气化改造概述
2.1 数控机床的主要功能
数控机床是实现机械加工、制造和生产中应用的最为广泛的一类机电设备。 数控机床依托数控化程序,实现对零部件的自动切削和加工。 但是目前我国仍然有超过近1000万台的数控机床,主要依靠手动控制完成切削加工,无法实现基本的电气化和自动化控制。 为此,本论文的主要的目的是基于PLC控制技术,实现数控机床的电气化改造,主要实现以下功能:
(1) 数控机床的所有电机、接触器等实现基于PLC的自动化控制;
(2)数控机床的进给运动由PLC控制自动完成,无需人工手动干预;
(3) 自动检测零部件切削过程中的相关参数,如加工参数、状态参数等等;
(4) 结合上位机能够实现对数控机床的远程控制,以达到无人值守的目的。
2.2 电气化改造的总体方案
结合上文对于数控车床的电气化、自动化改造的功能要求,确定了采用上位机与下位机结合的自动化改造方案。该方案总体结构分析如下:
(1) 上位机借助于工控机,利用工控机强大的图像处理能力,重点完成数控车床的生产组态画面显示,以及必要的生产数据的传输、保存、输出,同时还要能够实现相关控制指令的下达,确保数控车床能够自动完成所有切削加工生产任务。
( 2)下位机采用基于PLC技术的电气控制模式,由传感器、数据采集板卡负责采集数控车床的生产数据、环境数据、状态数据等所有参数,由PLC实现对相关数据的计算,并传输给上位机进行相关数据的图形化显示和保存;另一方面,PLC控制系统还接收来自于上位机的控制指令,实现对数控车床的远程控制。
(3) 对于数控车床最为关键的控制――进给运动的控制,利用PLC+运动控制板卡的模式实现电气化和自动化的控制。 具体实现方式为:选用合适的运动控制板卡,配合PLC的顺序控制,对进给轴电机实现伺服运动控制,从而实现对数控车床进给运动的自动化控制。
3 数控车床电气化自动控制改造的实现
3.1 系统改造结构设计
数控车床的电气化自动控制改造,其整体结构如下图1所示,其整体结构主要由以下几个部分构成:
3.1.1 底层设备
底层设备主要包括两个方面,首先是实现数控车床自动切削加工运转等基本功能的必要电气、机电设备,如电源模块、电机模块等,这些机电设备能够保证数控车床的基本功能的稳定可靠的实现;其次,底层设备还包括各类传感器,比如监测电机转速、温度的速度传感器和温度传感器,监测进给轴运动进给量的光栅尺等,这些传感类和数据采集类设备为实现数控车床自动化控制提供了基础数据源。
3.1.2 本地PLC站
本地PLC站主要负责接收底层传感设备传送过来的传感参数、状态参数及其他检测参数,通过内部程序的运算,判断整个数控车床的工作状态,并将其中的重点参数上传到远程控制终端进行数据的图形化显示、存储、输出打印等操作;另一方面,本地PLC站同时还接收来自于远程控制终端所下达的控制指令,比如停机、启动等控制指令,PLC站通过对相应执行器(比如电机)的控制,从而实现自动化控制的功能。
3.1.3 远程控制终端
远程控制终端主要是依赖于工控机实现的上位机数据管理和状态监控,需要专门开发一套面向数控车床加工、生产和自动控制的软件程序,以实现对数控车床的远程化、网络化、自动化控制,真正实现无人值守的功能。
3.2 PLC电气控制系统的设计实现
本研究论文以CK6140普通数量机床为具体研究对象,详细探讨其电气化、自动化控制的改造。 通过上文对机床改造方案和结构功能的分析,可以确定整个机床电气化、自动化改造,一共需要实现14个系统输入,9个系统输出。 结合控制要求,这里选用日本三菱公司的FX2N-48MR型PLC,输入回路采用24V直流电源供电方式。 根据对数控机床的各模块控制功能的分析,选用合适的接触器、继电器、开关、辅助触点等电气控制元件,与PLC共同实现对电气设备的控制,比如PLC通过接触器控制电机模块,PLC通过继电器控制电磁阀等部件,从而完成基于PLC控制的数控车床电气化改造。
4 结语
随着电气设备的越来越复杂,工业生产对于电气控制的要求也越来越高,基于PLC的自动化控制技术得到了广泛的应用,逐渐成为了当前工业自动化生产控制中的主流技术之一。 采用PLC技术最大的优势在于实现自动化控制同时具有较高的可靠性和抗干扰能力,极大的避免了由于采用单片机技术而造成的系统不稳定现象。 本论文结合电气控制详细探讨了PLC自动化技术的应用,给出了具体的系统设计实例,对于进一步提高PLC自动化技术的工业化应用具有很好的指导和借鉴意义。
参考文献:
什么是基于PLC的过程控制
基于PLC的过程控制是一种工业自动化技术,它利用可编程逻辑控制器(PLC)来实现对生产过程的监控、控制和管理。 PLC是一种专门为工业环境设计的数字计算机,它能够接收输入信号,根据预设的程序逻辑执行控制任务,并输出控制信号以控制工业设备。 在基于PLC的过程控制中,PLC扮演着核心控制器的角色。 它通过与传感器、执行器等现场设备连接,实时采集生产过程中的各种参数,如温度、压力、流量等。 PLC根据这些实时数据和预设的控制逻辑,对生产过程进行精确控制。 例如,在一个温度控制系统中,PLC可以根据温度传感器的反馈信号,通过控制加热或制冷设备的开关,使环境温度保持在设定的范围内。 与传统的继电器控制系统相比,基于PLC的过程控制具有更高的灵活性和可编程性。 PLC的控制逻辑可以通过修改程序来实现,而不需要更换硬件。 这使得PLC能够适应不同的生产环境和控制需求。 此外,PLC还具备强大的通信能力,可以与上级管理系统进行数据交换,实现远程监控和控制。 基于PLC的过程控制在许多工业领域都得到了广泛应用。 例如,在化工生产中,PLC可以实现对化学反应过程的精确控制,确保产品质量和生产安全。 在机械制造领域,PLC可以控制机床、流水线等设备的运行,提高生产效率和产品质量。 此外,PLC还在电力、水处理、食品加工等领域发挥着重要作用。 总之,基于PLC的过程控制是一种高效、灵活且可靠的工业自动化解决方案。 它利用PLC实现对生产过程的精确控制和管理,提高了生产效率和产品质量,降低了成本和安全风险。 随着工业技术的不断发展,基于PLC的过程控制将在更多领域得到应用和推广。
本文原创来源:电气TV网,欢迎收藏本网址,收藏不迷路哦!
添加新评论