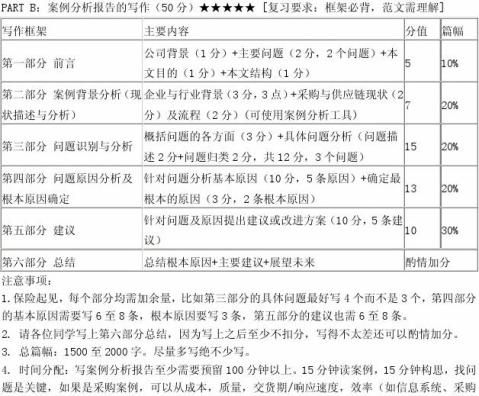
一、引言
在工业自动化领域,PLC(可编程逻辑控制器)编程技能至关重要。
热电阻信号作为常见的工业信号之一,其处理在PLC编程中占据重要地位。
本文将通过四个实战案例,详细介绍如何快速掌握热电阻信号PLC编程技能。
二、案例一:热电阻信号输入处理
背景:
某化工厂需要采集热处理设备的温度数据,采用热电阻信号进行传输。
任务:
1. 接收热电阻信号;
2. 将信号转换为数字量;
3. 在HMI上显示温度数据。
实战步骤:
1. 在PLC中输入端配置热电阻信号模块,选择适当的信号类型(如Pt100);
2. 使用PLC内置A/D转换功能,将热电阻信号转换为数字量;
3. 通过通信模块,将温度数据上传至HMI进行显示。
关键点:
1. 确保热电阻信号模块与现场设备匹配;
2. 注意信号转换的精度和稳定性;
3. 合理配置HMI界面,方便操作人员查看。
三、案例二:热电阻信号控制加热设备
背景:
某机械设备需要按照设定的温度曲线进行加热,采用热电阻信号进行温度检测和控制。
任务:
1. 采集热电阻信号,获取实时温度数据;
2. 根据温度数据,控制加热设备的开关;
3. 实现温度曲线的调整功能。
实战步骤:
1. 在PLC中配置热电阻信号模块,采集温度数据;
2. 使用PLC的PID控制功能,根据设定温度与实际温度的差值,计算控制输出;
3. 通过输出模块,控制加热设备的开关;
4. 在HMI上实现温度曲线的调整功能,通过通信模块上传至PLC。
关键点:
1. 确保PID控制参数的准确性;
2. 注意加热设备的安全控制,避免超温或欠温;
3. 合理设计温度曲线调整功能,满足生产需求。
四、案例三:热电阻信号的校准与补偿
背景:
由于现场环境的温度变化、线路阻抗等因素,热电阻信号可能产生误差,需要进行校准与补偿。
任务:
1. 对热电阻信号进行校准;
2. 实现温度补偿功能。
实战步骤:
1. 在实验室条件下,测量热电阻信号的输出值,与标准值进行对比,计算误差;
2. 根据误差值,调整PLC中的参数,对热电阻信号进行校准;
3. 在PLC中实现温度补偿功能,根据环境温度变化,自动调整输出值。
关键点:
1. 确保校准环境的准确性;
2. 合理选择补偿算法,提高测量精度;
3. 定期检查校准,确保系统稳定性。
五、案例四:多通道热电阻信号处理与优化
背景:
某生产线需要同时处理多个设备的热电阻信号,以提高生产效率和产品质量。
任务:
1. 接收多个通道的热电阻信号;
2. 对信号进行优化处理;
3. 实现数据的实时分析与优化调整。
实战步骤:
1. 在PLC中配置多个热电阻信号模块,接收各通道的信号;
2. 使用滤波、平滑等处理方法,提高信号的稳定性与准确性;
3. 通过PLC的数据处理功能,实现实时数据分析,如最大值、最小值、平均值等;
4. 在HMI上展示数据分析结果,方便操作人员实时监控与调整。
关键点:
1. 确保各通道信号的独立性,避免相互干扰;2 . 优化处理算法的选择应满足实时性与准确性要求;3 . 合理设计HMI界面,方便操作人员实时监控与调整。六、总结通过这四个实战案例的分析与讲解,相信读者已经对热电阻信号PLC编程技能有了初步的了解和掌握。在实际应用中,还需要根据现场情况灵活调整和优化程序,不断提高自己的技能水平。同时,也需要注意安全控制,确保系统的稳定运行。希望本文能对你有所帮助,谢谢阅读!
本文原创来源:电气TV网,欢迎收藏本网址,收藏不迷路哦!
添加新评论