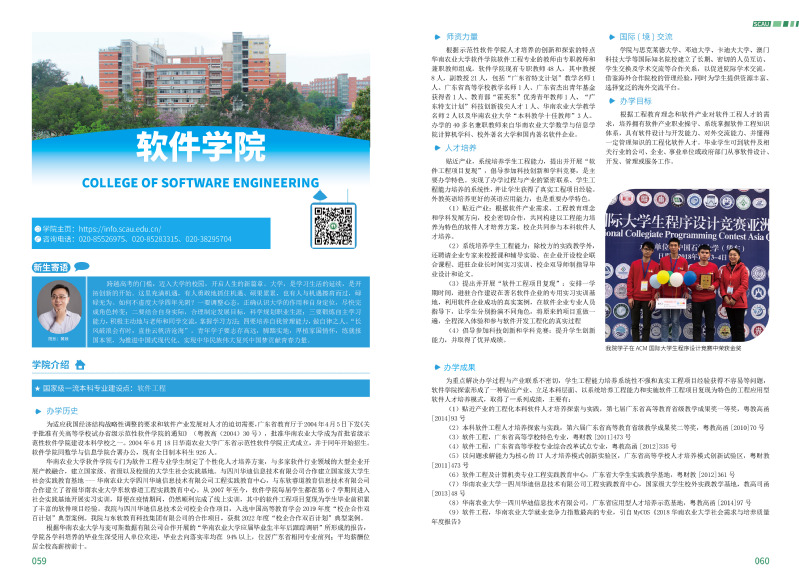
一、引言
随着工业自动化水平的不断提高,PLC(可编程逻辑控制器)在生产线上的作用日益凸显。
松下PLC作为市场上的知名品牌,其转换程序设计对于提高生产效率、降低成本具有重要意义。
本文将详细介绍如何优化和完善松下PLC转换程序设计,帮助工程师和自动化技术人员提高工作效率,减少错误。
二、松下PLC转换程序设计的现状
当前,松下PLC转换程序设计已经广泛应用于各类生产线中,但在实际应用过程中仍存在一些问题。
例如,程序结构不够优化,导致运行效率低下;部分功能实现不够完善,影响生产线的自动化程度;PLC与现场设备之间的通信不够稳定等。
针对这些问题,本文将从以下几个方面展开讨论。
三、优化松下PLC转换程序设计的策略
1. 优化程序结构
(1)模块化设计:将PLC程序划分为若干个功能模块,每个模块负责实现特定的功能。
这样可以使程序结构更加清晰,便于维护和修改。
(2)减少不必要的指令:精简程序中的冗余指令,提高程序的运行效率。
(3)使用高效的算法:在编写PLC程序时,应尽量采用高效的算法,以提高数据处理速度和准确性。
2. 完善功能实现
(1)增加自适应功能:为了提高PLC对不同生产环境的适应性,应增加自适应功能,使PLC能够根据生产线的实际情况自动调整参数。
(2)优化数据处理能力:为了提高生产线的自动化程度,应优化PLC的数据处理能力,实现对大量数据的实时处理和分析。
(3)增强通信功能:为了提高PLC与现场设备之间的通信稳定性,应增强PLC的通信功能,支持更多的通信协议和接口。
3. 加强调试和维护
(1)采用仿真调试:在PLC程序开发过程中,应采用仿真调试的方法,模拟实际生产线的运行情况,以便及时发现和纠正程序中的错误。
(2)建立完善的维护体系:建立完善的PLC维护体系,定期对PLC进行检查、维护和升级,确保PLC始终处于良好的工作状态。
四、松下PLC转换程序设计的实践应用
为了更好地说明优化和完善松下PLC转换程序设计的实际应用,本文将结合实际案例进行介绍。
例如,在某汽车生产线上,通过对松下PLC转换程序进行优化和完善,提高了生产线的自动化程度,降低了生产成本。
具体实践包括:对PLC程序进行模块化设计,优化程序结构;增加自适应功能,提高PLC对不同生产环境的适应性;优化数据处理能力,实现对大量数据的实时处理和分析;增强通信功能,提高PLC与现场设备之间的通信稳定性。
通过这些实践应用,取得了显著的效果,提高了生产线的运行效率和产品质量。
五、结论
本文详细讨论了如何优化和完善松下PLC转换程序设计,包括优化程序结构、完善功能实现和加强调试和维护等方面。
通过实际案例的介绍,展示了优化和完善松下PLC转换程序设计在生产线上的重要作用。
工程师和自动化技术人员在实际工作中,应根据本文提供的策略和方法,对松下PLC转换程序进行优化和完善,提高工作效率,减少错误,为生产线的稳定运行和高效生产做出贡献。
本文原创来源:电气TV网,欢迎收藏本网址,收藏不迷路哦!
添加新评论