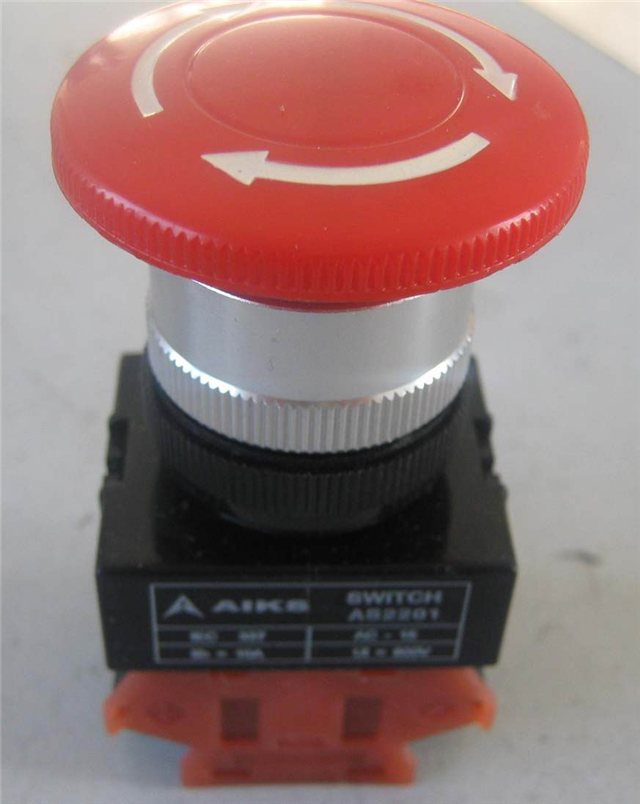
简介
在工业自动化中,PLC(可编程逻辑控制器)是控制机器和过程的关键设备。为了确保安全和可靠的运行,必须对 PLC 程序进行定期检查,尤其是对急停功能的检查。
本文将探讨 PLC 急停检查流程,并深入剖析>急停输入:一个数字输入点,接收来自急停按钮或其他设备的信号。
典型的急停逻辑将包括以下步骤:
- 当急停输入激活时,急停位被置位。
- 急停逻辑执行,将急停位与其他条件(如启用位)相结合,以确定是否触发急停。
- 如果急停条件为真,则激活急停输出,导致机器或过程进入安全状态。
PLC 急停报警解除
急停报警通常需要通过以下步骤解除:
- 清除急停条件:排除导致急停的物理或逻辑问题。
- 复位急停位:通过编程软件或 PLC 本身,手动复位急停位。
- 重新启动 PLC:在某些情况下,可能需要重新启动 PLC 以完全解除急停报警。
结论
定期检查 PLC 急停功能对于确保工业自动化系统的安全和可靠运行至关重要。通过遵循本文概述的检查流程,并深入了解 PLC 程序中的急停机制,我们可以确保 PLC 系统能够在关键时刻正常响应并保护人员和设备的安全。
除了定期检查之外,良好的编程实践也是至关重要的。PLC 程序员应该遵循适当的编码标准,并对急停功能进行彻底的测试。通过遵循这些最佳实践,我们可以最大限度地减少急停功能故障的风险,并确保工业自动化系统的安全和可靠操作。
日常维护与检查 3.1 系统日常维护项目 3.1.1 检查控制室、机房的空调工作是否正常。 3.1.2 检查环境温度、湿度是否在规定的范围内。 3.1.3 检查系统处理器、电源模件、通讯模件、I/O模件和电池状态指示灯是否正常、有无故障报警,并及时处理。 3.1.4 检查所有电缆连接件、插头、卡件有无松动或破损的现象。 3.1.5 检查系统风扇、机柜风扇运行是否良好。 3.1.6 每月对系统做清洁工作,包括对机箱表面、软盘驱动器、键盘、鼠标和屏幕等进行清洗。 3.1.7 每月对风扇、过滤网清扫,保障系统运行在良好的环境下。 3.2 故障诊断与处理 3.2.1 系统故障处理的步骤和所要注意的事项 3.2.1.1 故障处理前首先听取工艺人员反映的情况。 3.2.1.2 观察故障现象,观察画面,检查各模件LED指示状态,查设备运行状态。 3.2.1.3 检查接线、电缆、转接插件是否松动。 3.2.1.4 调出设备自诊断画面,观察由自诊断显示的故障代码,分析判断故障原因。 3.2.1.5 必要时进入Rslongix5系统,进行在线状态监控。 3.2.1.6 根据判断结果,与工艺人员联系并办理相关手续后,采取相应的处理措施,更换设备或模件等。 3.2.1.7 更换模件时,注意防静电措施,最好带上绝缘护腕和手套。 注意更换的模件是否与原模件完全相同,并确认模件地址及跨接线正确。 3.2.1.8 设备、卡件安装后,要检查其功能;与工艺联系确认后恢复系统,观察系统工作是否正常。
本文原创来源:电气TV网,欢迎收藏本网址,收藏不迷路哦!
添加新评论