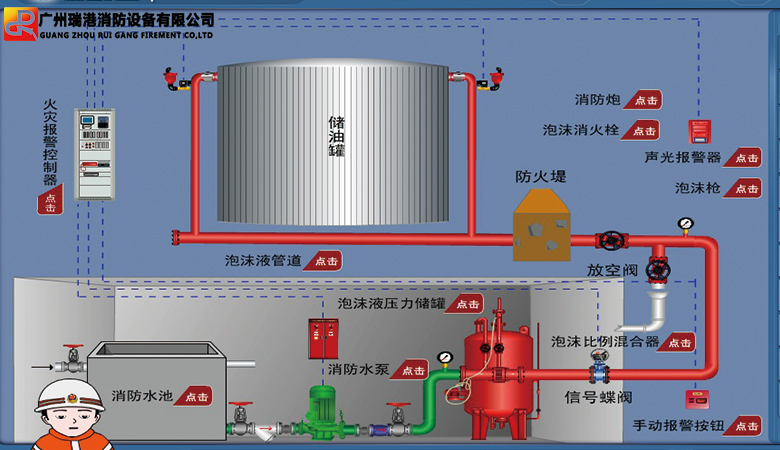
引言
在工业生产中,罐体冷却系统是一种至关重要的设备,用于控制和调节罐体内的温度,确保产品质量和生产效率。PLC(可编程逻辑控制器)是用于自动化控制系统中的工业计算机,负责执行控制程序和监控系统状态。PLC控制程序设计
PLC 控制程序是罐体冷却系统自动化控制的关键组成部分。该程序根据输入的传感器数据和外部控制命令,执行以下主要功能:1. 温度控制
从温度传感器获取罐体温度数据。与设定值进行比较,计算温度偏差。根据偏差调节冷却阀门开度,控制冷却介质流量。确保罐体温度稳定在设定范围内。2. 压力控制
从压力传感器获取罐体压力数据。与设定值进行比较,计算压力偏差。根据偏差调节排气阀门开度,控制罐体压力。保持罐体压力处于安全范围内。3. 液位控制
从液位传感器获取罐体液位数据。与设定值进行比较,计算液位偏差。根据偏差调节进料阀门开度,控制罐体液位。防止罐体溢出或缺料。4. 系统监控
监控系统组件的状态,如泵、阀门、传感器等。检测故障或异常情况,并发出报警。记录系统运行数据,便于故障排除和维护。PLC 控制系统架构
罐体冷却系统 PLC 控制系统通常由以下组件组成:PLC 主机:执行控制程序,处理输入/输出数据。输入/输出模块:连接传感器和执行器,进行数据采集和控制输出。人机界面(HMI):提供人机交互界面,显示系统状态和参数设置。传感器:监测温度、压力、液位等参数。执行器:控制冷却阀门、排气阀门、进料阀门等。控制程序逻辑
罐体冷却系统 PLC 控制程序的逻辑通常遵循以下步骤:1. 初始化:加载控制程序,设置系统参数和变量。 2. 数据采集:从传感器采集温度、压力、液位等数据。 3. 计算偏差:将采集的数据与设定值进行比较,计算偏差。 4. 控制输出:根据偏差,调节冷却阀门、排气阀门和进料阀门的开度。 5. 系统监控:检查系统组件的状态,检测故障或异常情况。 6. 报警处理:当检测到故障或异常时,发出报警并记录事件。 7. 数据记录:定期记录系统运行数据,便于故障排除和维护。结论
罐体冷却系统 PLC 控制程序是实现自动化控制和优化罐体温度、压力和液位的核心组件。通过仔细设计和实施,可以提高系统效率、产品质量和安全性。冷却系统由水泵、散热器、冷却风扇、节温器、补偿水桶等组成。 冷却系统的作用是使发动机在所有工况下都保持在适当的温度范围内。 冷却系统既要防止发动机过热,也要防止冬季发动机过冷。 冷却系统组成的具体介绍:水泵:给冷却液加压,保证冷却液在冷却系统中循环。 离心水泵广泛应用于汽车。 散热器:由进水室、出水室和散热器芯组成。 冷却液在散热器芯中流动,而空气体从散热器芯中流出。 空的热冷却液通过向空气散热变冷,而冷空气空通过吸收冷却液的热量变暖,所以散热器就是热交换器。 冷却风扇:风扇转动时,吸入空空气,使其通过散热器,从而增强散热器的散热能力,加快冷却液的冷却速度。 恒温器:控制冷却剂流动路径的阀门。 它根据冷却液的温度打开或关闭冷却液到散热器的通道。 补偿桶:冷却液受热膨胀时,部分冷却液流入补偿桶;冷却液冷却下来,一部分冷却液被吸回散热器,所以冷却液不会溢出。
本文原创来源:电气TV网,欢迎收藏本网址,收藏不迷路哦!
添加新评论